A pick and place machine to increase production efficiency and flexibility in confectionery packaging
- High performance and gentle product handling
- Maximum efficiency and flexibility due to special “on the fly” product count modification
- 3D scanners ensure precise picking
Requirements
Needed: a robotics-based packaging line instead of semi-automated equipment
Sweet Candy Company is a fifth-generation family-owned and operated American confectioner, based in the heart of Salt Lake City, Utah. The company, also famously called “Sweet’s”, distributes more than 250 quality candy items nationally and internationally in bulk, bags and boxes. Sweet’s is well known for its quality candy and world-class customer service.
Sweet’s turned to Schubert with the challenge to package one of their signature brands, their jelly filled chocolate sticks. Sweet Candy Company has been making this product for over 90 years and has gone through different alterations of its packaging. The confectioner’s demand was increasing for chocolate jelly sticks and they needed to increase the throughput of the line to be able to add on another shift to satisfy the new customers. The existing equipment was semi-automated, which required lots of human intervention and manipulation. In addition, it was only packing about 50% of the upstream product, the other 50% needed to packed by hand.
The confectioner needed a robotics based packaging system to handle the larger production volume that is also able to flexibly adjust the amount of products per box. At the same time, Sweet’s focused on high mechanical stability, outstanding customer service and training to enable easy machine system operation.
Solution
Pre-erected trays for quality chocolate sticks
Sweet Candy Company produces jelly filled chocolate sticks in different flavours. The flavours are dark chocolate or milk chocolate sticks, filled with cherry, blueberry, orange, raspberry, or other seasonally flavoured jellies. The product is sold by weight in 10.5 oz boxes, and not by count. One single box contains approximately 32-34 sticks per box. Sweet Candy Company sells their chocolate sticks not only for their own labels, but also for other labels in differently labelled boxes.
Schubert succeeded in fully satisfying Sweet Candy Company with a robotic solution that solved their labour equation and allowed the confectioner to make its anticipated change in production throughput.
The quality chocolate sticks are packaged into pre-erected trays. Special to this packaging task is that a layer of wax paper is placed between the two layers of products. Another important feature is the “on the fly” product count modification. The bottom layer has a fixed number of products, and the top layer can be adjusted by +/-1 products during production. This adjustment is necessary as the product is sold by weight and not by count.
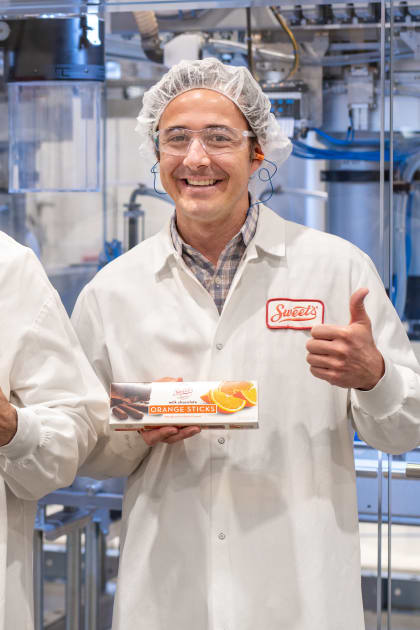
Schubert became a very obvious choice, and I don’t regret it one bit. It’s provided everything we’ve expected.
Rick Kay
President/CEO Sweet Candy Company, June 2023
Technical details
- Pickerline with 16 vision guided F4 robots
- “On the fly” product count modification to adjust the top product layer by +/-1 products during production
- Two layers of products divided by wax paper
Unique: Schuberts machines are capable of adjusting the number of products per carton, triggered by weight feedback
1920 chocolate sticks transition into Sweet’s new packaging system from an 860 mm wide cooling tunnel belt. Within the packaging system, the products are pre-grouped in a multi-pick fashion in layer formations of 15-17 sticks by 16 vision guided F4-axis scara type robots. Unique to this system is that it is capable of adjusting the number of products per carton, triggered by weight feedback. The adjustment can be done during production via a manual input at the machine HMI.
Previously erected carton bases are indexed into a transport chain and a F4 robot loads the carton trays with the first pre-grouped layer. In the next step a wax paper is placed on top of the first layer, also executed by a F4 robot. Then occurs the loading of the second product layer onto the wax paper. And finally, the box is closed by a F4 robot placing the pre-erected lid onto the fille carton bottom.
Rick Kay
“Their training disciplines were something I hadn't experienced from a supplier before,” Kay says. “Beyond the equipment itself, training certainly helped differentiate them. Just the idea that we're going to get the support we needed was important since we're out in the middle of nowhere. Their engagement with our maintenance team, with our operators, and with our management was remarkable. To me, that's a differentiator in future projects; they're at the top of the leaderboard on who we want to talk to. If you're going to be in the food business domestically and be competitive, especially confection business, you need throughput. You've got to run lean and mean. Downtime kills you.”
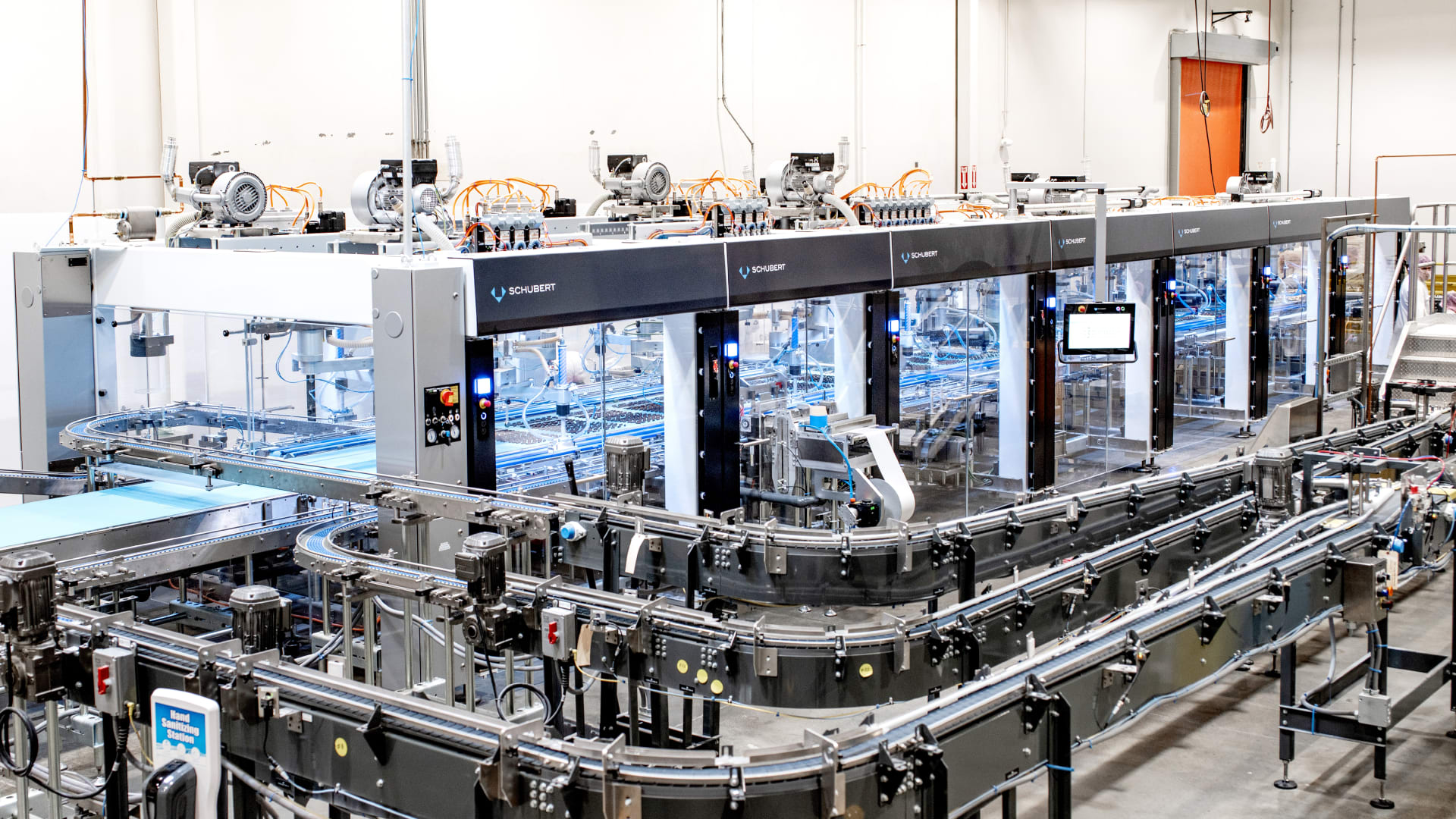
The robotic solution of Schubert, a pickerline with 16 vision guided F4 robots, allowed the confectioner to make its anticipated change in production throughput.
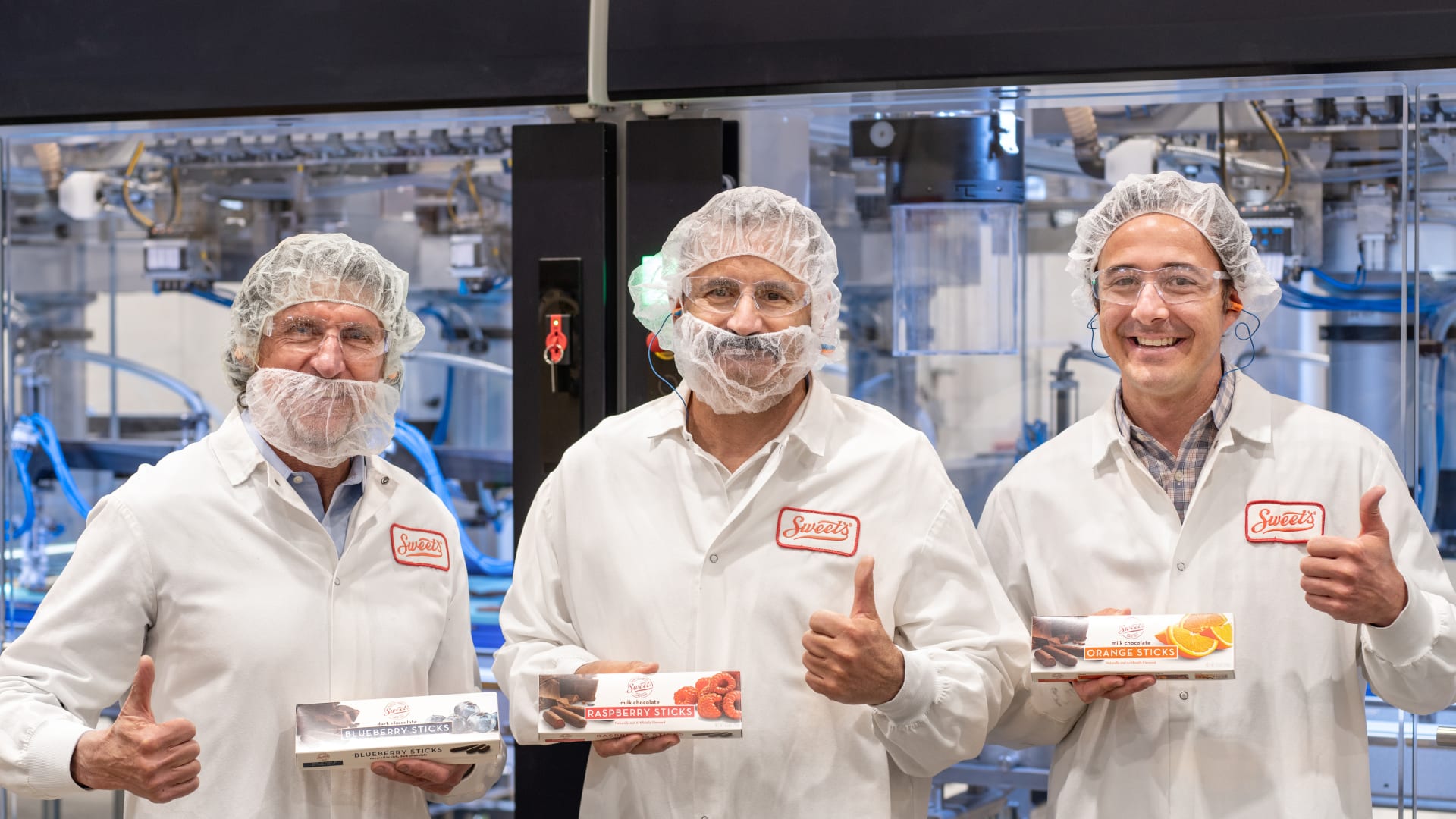
Armin Klotz, Sales Account Manager at Schubert together with Geoffrey Dzuida, VP Operations at Sweet Candy Company and Rick Kay, President / CEO at Sweet Candy Company.
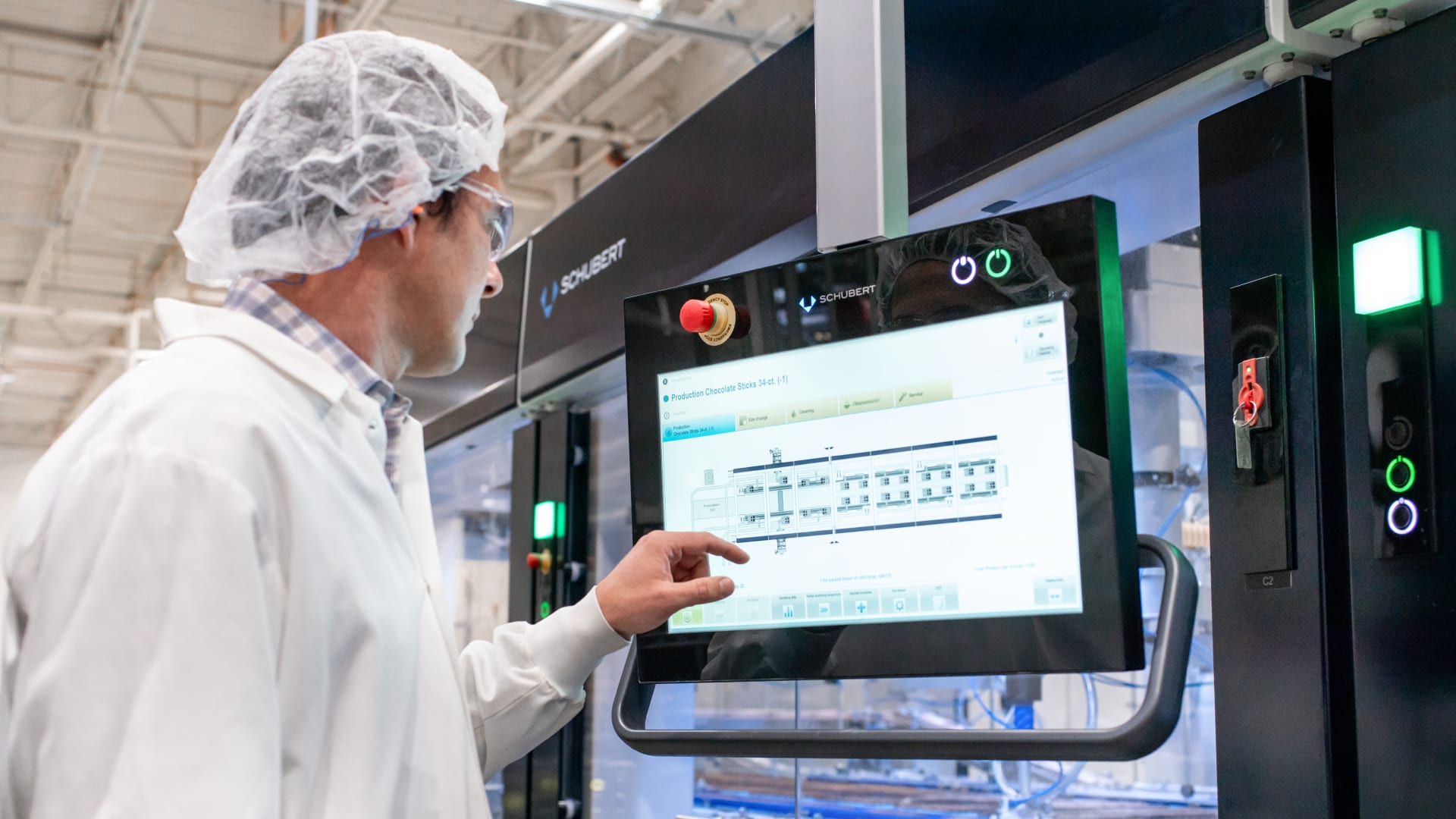
: Unique: The “on the fly” product count modification which can be done during production via a manual input at the machine HMI.
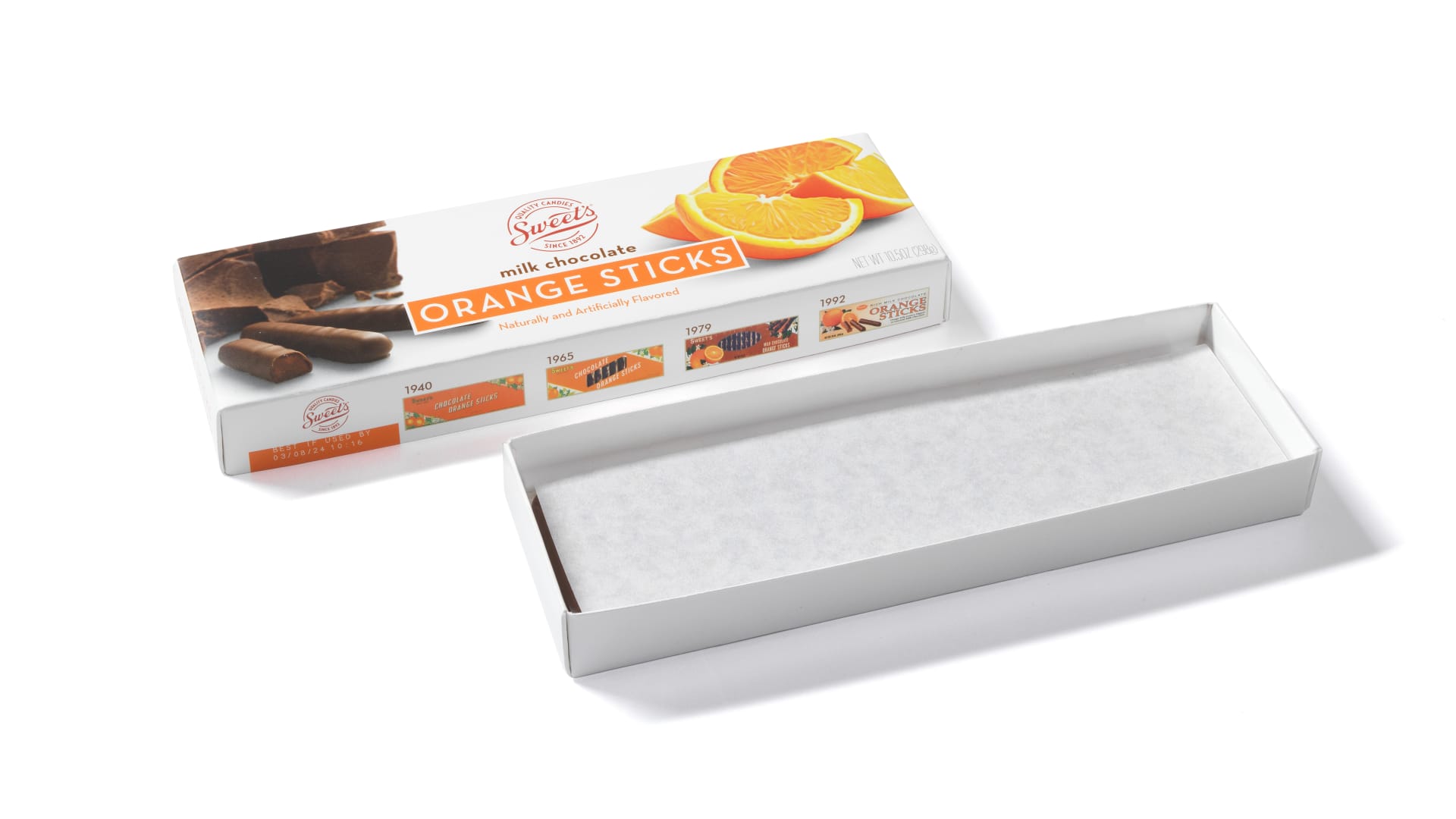
The erected carton bases contain a wax paper, which is placed on top of the first layer, executed by a F4 robot.