Using a Schubert bar packer as an example, the TLM Comfort Feeder demonstrates the many advantages of the recently developed feeder directly from the pallet when packing into cartons: The entire process, from the removal of the flat blanks to the erected packaging, is automated and very compactly integrated into a single sub-machine. It is seamlessly connected to the downstream packaging process, for example via Transmodul, belt or vacuum conveyor, depending on requirements. The TLM Comfort Feeder is the logical extension of Schubert’s signature concept of a fully integrated and controlled packaging process. With single-lane processing of each carton blank, the performance of the machine-integrated robots is ideally used so that a cycle rate of 60 packs per minute can be achieved. At the same time, the infeed and erecting process remains very lean, which considerably reduces the size and weight of the robot tools and the number of glue nozzles required to glue the blanks.
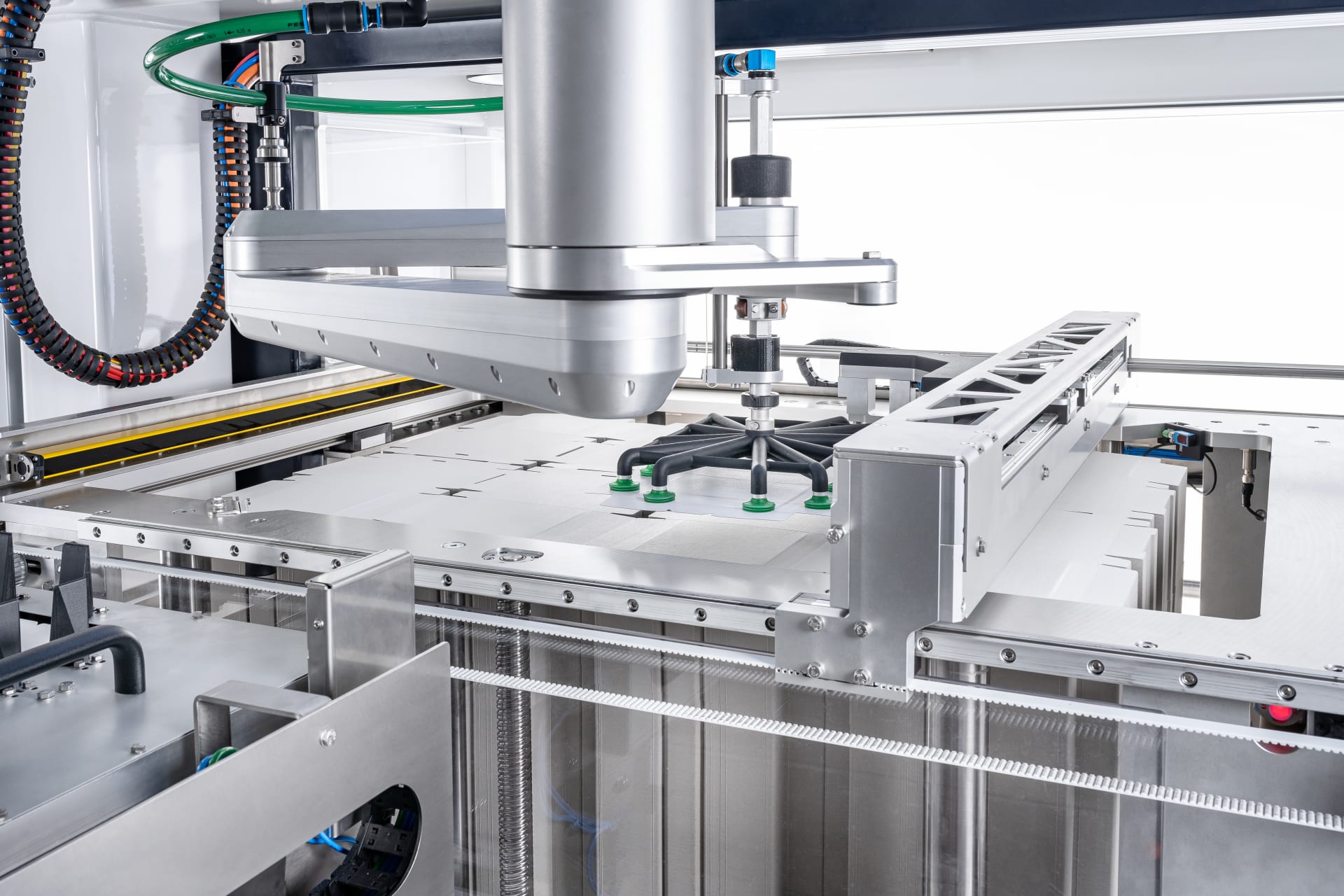
When feeding directly from the pallet, an F4 robot pulls each blank individually from the sheet.
Single-lane feeding and erecting directly from the pallet
For feeding, the pallet with all the blank sheets is simply placed into the machine. The blanks are pre-cut and only connected at a few predetermined breaking points to form a sheet. Blank sheets prepared in such a way are easily supplied by packaging manufacturers on request and eliminate the need for interleaving sheets on the pallet. For removal, a spacer then fixes the cardboard sheet in place, while an F4 robot pulls each blank directly from the sheet one by one and deposits it into a vertical magazine that serves as a buffer. During this process, the pallet is gradually lifted until it reaches the last sheets. A camera also monitors the corner of each top sheet so that the robot can accurately access each blank.
In the new A6 erector, each blank is pulled individually from the bottom of the buffer and transferred to a pusher that transports it past the gluing unit to a folding box. There, a punch sucks up the blank, pushes it through the folding box for erecting and places it onto the transport system. The unit achieves a high output of 60 blanks per minute in spite of its streamlined single-lane design. It can also be used in Schubert machines without infeed from the pallet, but with a vertical magazine.
The subsequent robot-assisted filling of the cartons continues to run in a single lane in the bar packer. Only when sealing the cartons does an F2 robot take over two cartons at a time – to maintain the output rate of 60 products per minute. Equipped with Schubert Motion software for optimised movements, this robot also operates at high performance.
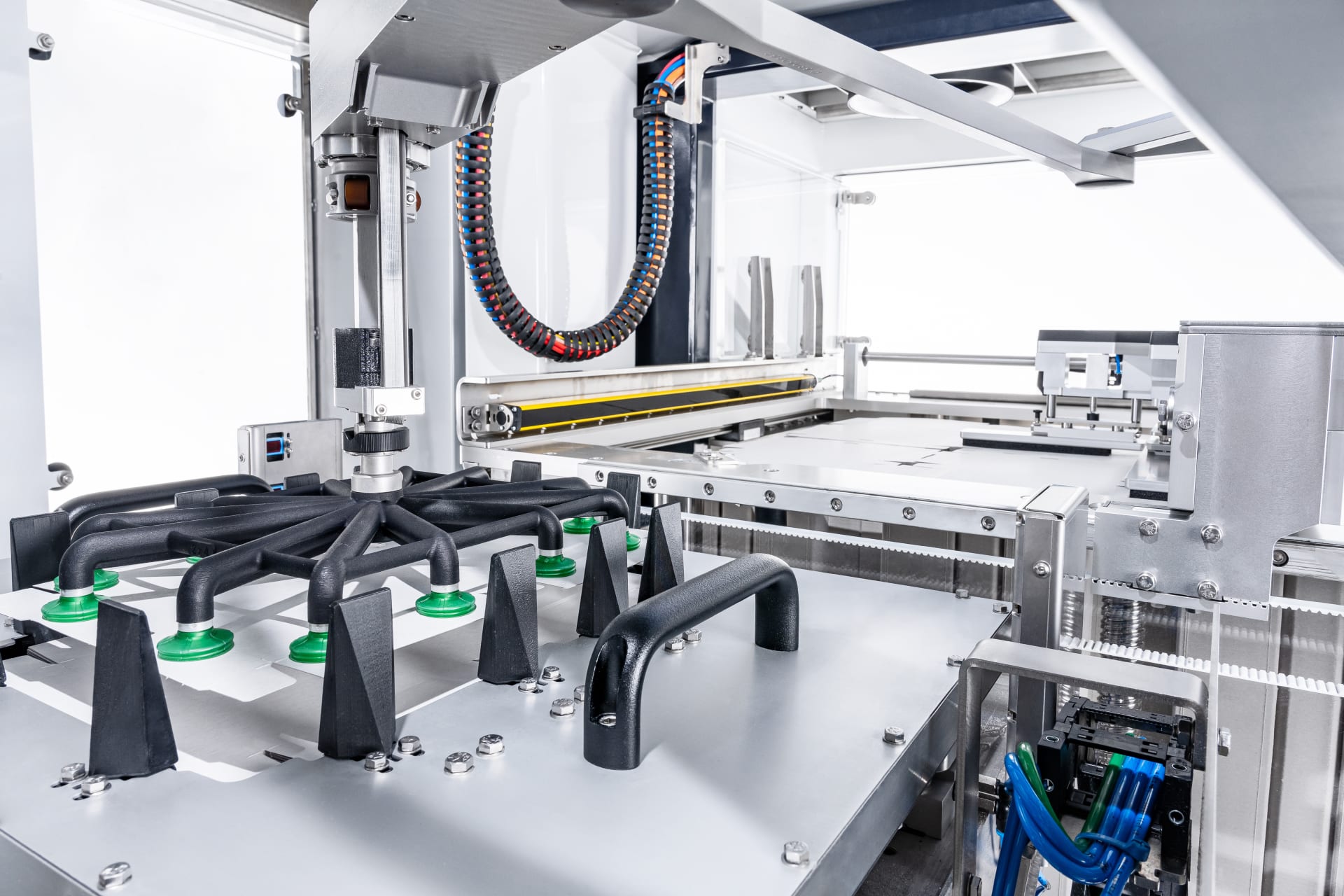
After being removed from the blank sheet, the flat blanks are placed directly into the A6 erecting unit’s magazine and erected in a single lane at a rate of 60 cycles per minute.
A cost-effective, high-performance concept in the smallest of spaces
The combination of an all-new sheet infeed, high erecting capacity as well as loading and sealing in a small space offers Schubert customers a uniquely advantageous machine concept for the bar packer. The machine’s performance density in the smallest possible space – known as the “TLM Power Compact” – saves a great deal of space in production. The new infeed makes operation extremely simple and the lightweight, small robotic tools can be easily handled by one person. Until a pallet is emptied, the machine can work for four to five hours without refilling. When a full pallet is exchanged, the buffer takes over the feeding, so that a machine stop is not required. The prepared blank sheets save weight during transport and also enable the packaging to be optimised to material-efficient formats. Many advantages make the integration of the TLM Comfort Feeder into a high-speed Schubert packaging machine a powerful and cost-effective proposition for manufacturers in a wide range of industries.
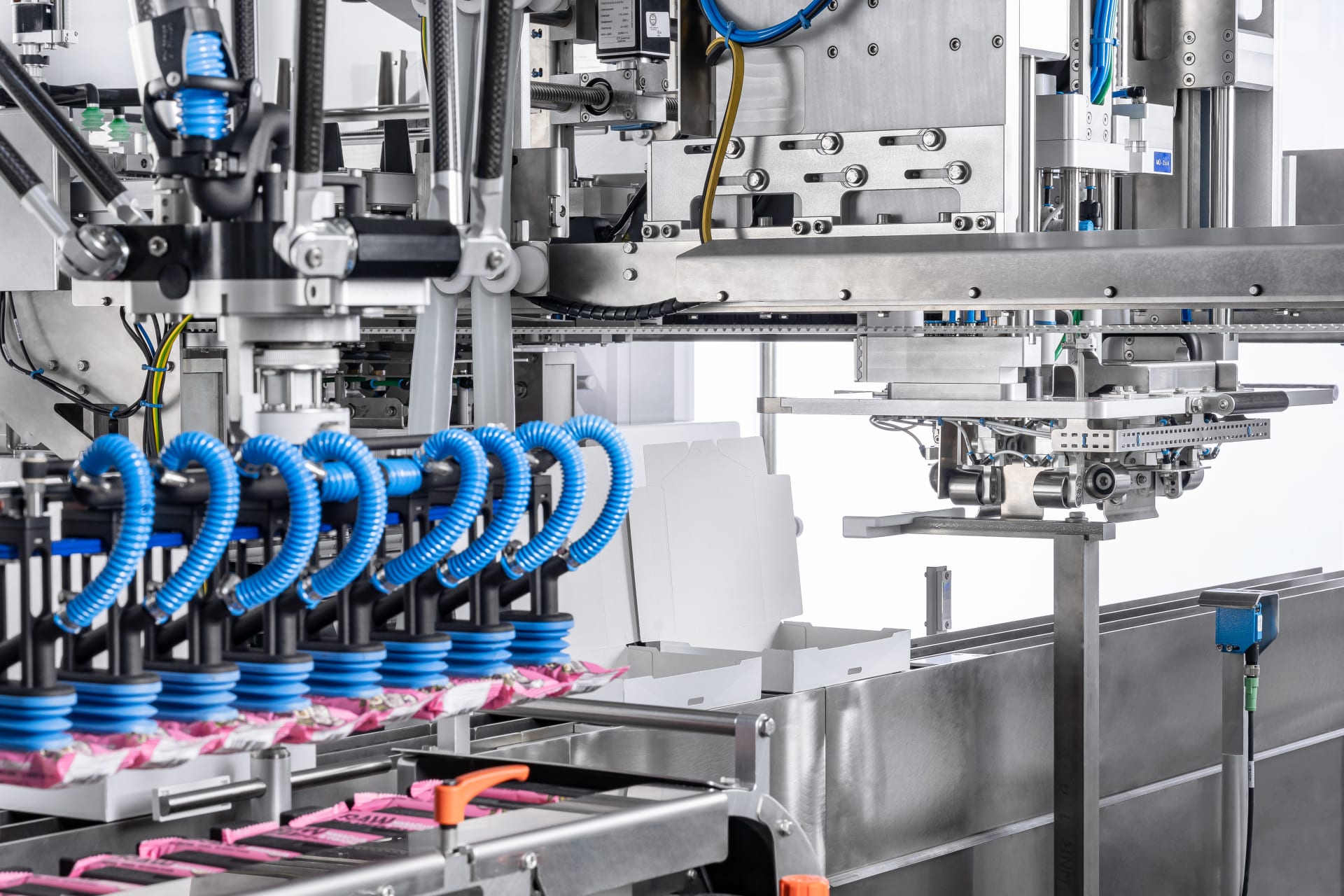
A very lightweight 3D-printed filling tool on the T4 robot ensures that two cartons are filled at a time.