For close to 50 years, the Gerhard Schubert company’s flexible packaging machines have been based on a sophisticated modular system. Each TLM machine is modularly designed, i.e. it brings together seven standard components, a frame, 2-, 3- and 4-axis robots, control technology, image processing and a Transmodul. Each system consists of multiple machines. With this high degree of standardisation, greatly reduced machine complexity and mechanics, intelligent control systems and exchangeable tools, Schubert is bringing to life its TLM philosophy while implementing an essential lean management principle: reducing waste in machine manufacturing and utilisation.
Everything that is good for the customer is also good for the company
The moving assembly line, introduced by Henry Ford in 1908, refers to a mode of production whereby the product is moved along rails and all steps are timed. Ideally, all departments work in a synchronised manner – with components for assembly ‘flowing’ through production.
The introduction of the moving assembly line represented a paradigm shift at the Schubert company. It was initially introduced for basic components and was then continuously expanded over the following years. Over time, employees recognised the benefits it delivered, such as time savings, shortened throughput times and higher delivery reliability. Significant savings potential became obvious and was often accompanied by improvements in quality.
Today, pre-assembly at Schubert requires a six-day throughput time, i.e. after six days, a pre-assembled machine part leaves the assembly line. Subsequently, the pre-assembled machine parts are brought together into a packaging system in final assembly and different formats are run
Fixed priorities through sequence planning
In order to achieve production flow, a sequence of tasks is determined. Due to a fixed sequencing, and unlike with other job-oriented work approaches, there are no order peaks. Every week, there is a constant production volume at Schubert that is moved throughout the company. The priorities across all departments are identical. The coordination of deadlines takes place through central planning control through to departmental controls, such as pre-assembly, assembly manufacturing or the welding shop.
The just-in-sequence principle implies that the required materials are made available on the line within a product’s final assembly process. The suppliers pre-pack and deliver materials exactly when needed.
Schubert’s own production planning and control system (PPS) called Saturn is the basis for this exact timing. Company founder Gerhard Schubert himself developed the system’s main features and Managing Director Ralf Schubert developed the required programmes.
The PPS enables planning based on a parts list that is generated automatically. Building works with the TLM configurator, where all standard components are stored in the form of a selection catalog. These components are used by Schubert designers to configure the machine using a CAD programme. The system creates a parts list of required components, which migrates to the PPS.
By linking the TLM configurator with the Saturn PPS system and the automatic creation of a parts list, Schubert achieves a higher level of standardisation than most competitors. “This way, everyone in the company is aware of when each customer order is processed,” explains Marcus Schindler, Head of Parts Production at Schubert. “Each department has precise specifications as to when they must deliver something. This guarantees a high level of transparency across all departments, enabling any potential problems to be identified early and resolved.”
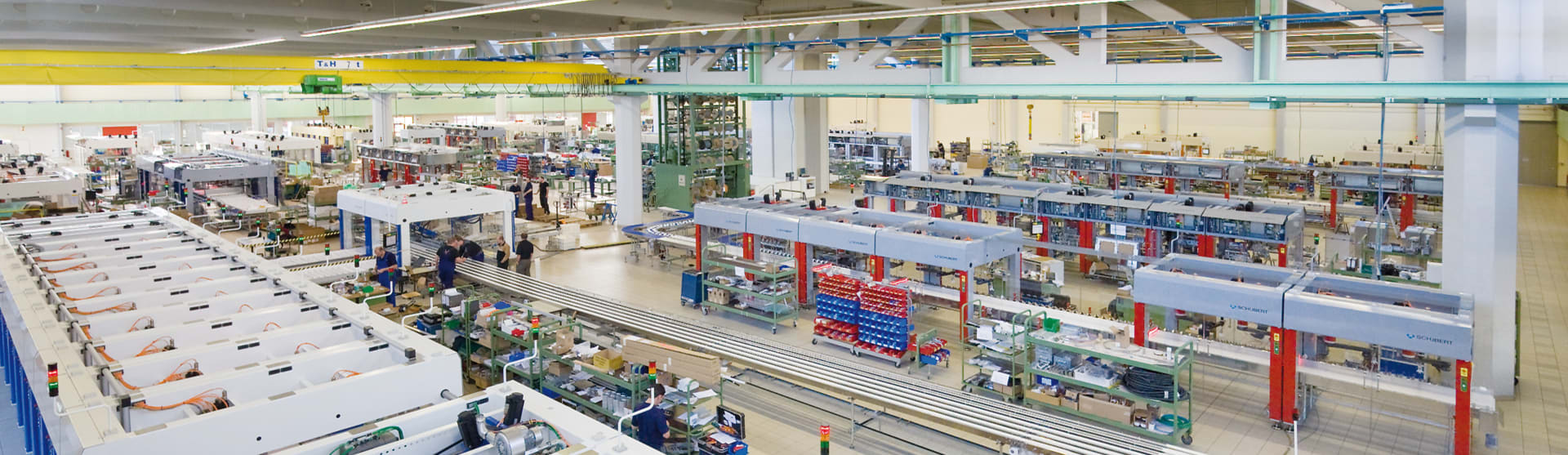
The configuration of the assembly hall follows the principles of a highly efficient workflow.
High employee motivation
Organisation and cleanliness in all work areas will always be very important at the Schubert company. Work stations are clean, safe and largely standardised. We believe that employees can only feel comfortable and do excellent work in a clean and well organised environment. As well, organisation bears witness to professional expertise while reducing errors.
All this calls for a high level of employee motivation. Unlike other companies, Schubert employs only skilled workers, rather than temporary, semi-skilled or apprentice workers. Through their long-term employment at Schubert, the staff identifies with the company and takes on responsibility – an important pillar of our corporate philosophy.
Schubert is continuously working towards further enhancing the synchronization of production with assembly, so that parts are produced exactly as they are required by assembly – always driven by the reduction of throughput times and the ultimate objective of supplying customers even more quickly and more reliably.