Until now, the final assembly of Schubert’s packaging lines was carried out in two halls on the factory premises. In the future, one of these will be used for the expansion of pre-assembly. The new Hall 3 will increase the final assembly area by 30 per cent. Due to the very favourable order books, Schubert expects that half of the space in the new hall will be occupied by the end of the current year. The new building fits seamlessly into the existing production complex, and it stands out not only with its impressive size but also with its airy, modern design with six-metre-high glass façades on three sides of the building. From the pre-assembly area, which is directly connected to the warehouse and logistics centre, it is only a few metres to the new final assembly area. The new hall will expand the final assembly capacity by 30 per cent, which Schubert expects to significantly increase its turnover. Ralf Schubert, Managing Partner at Gerhard Schubert GmbH, explains: “With our innovative top-loading (TLM) packaging machines, we currently generate an annual turnover of some 300 million euros. By expanding our production capacity, this could reach up to 400 million euros.”
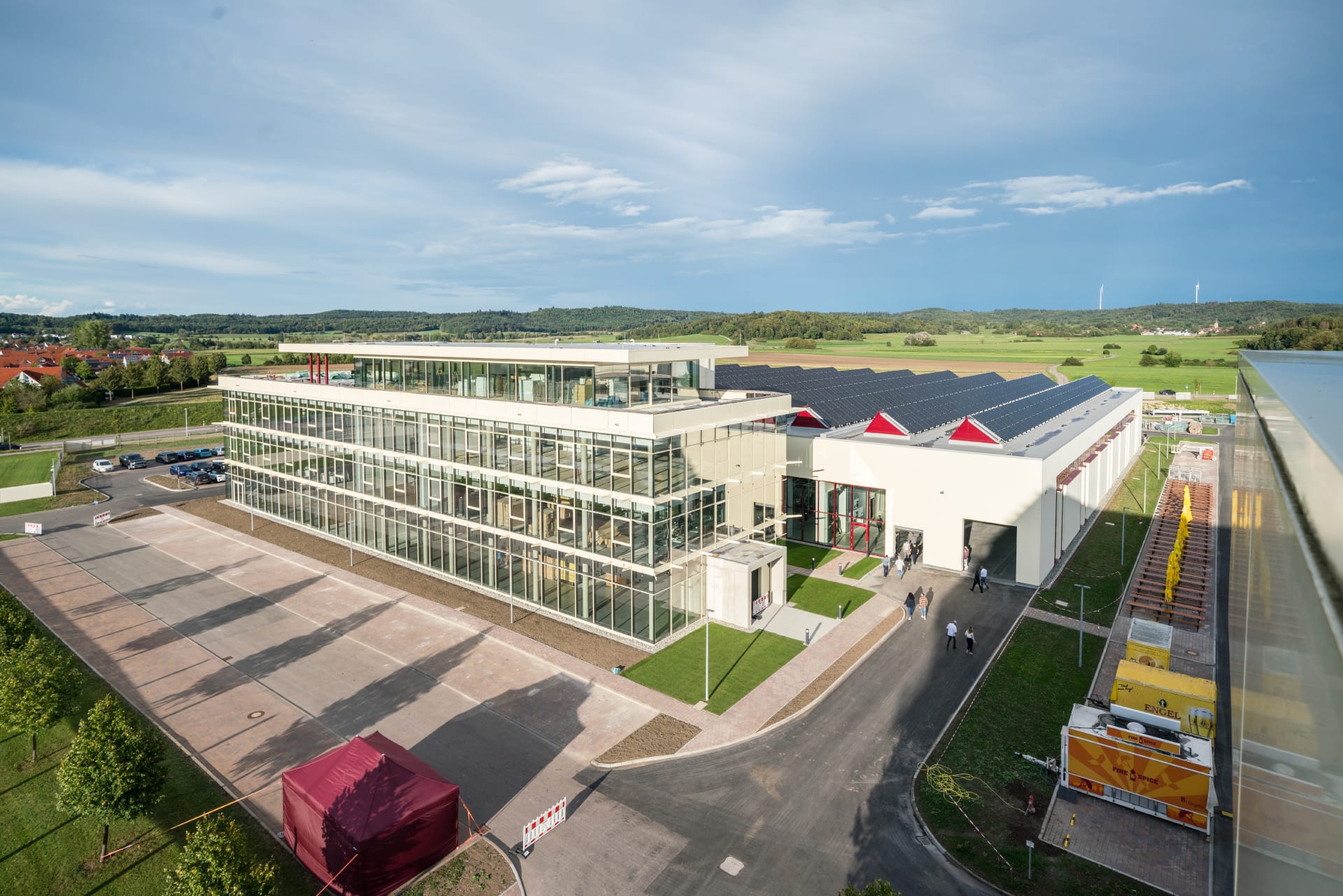
The newly built complex, consisting of an office building (in the foreground) and a final assembly hall.
Opening of the adjacent office building planned for early November
The new office wing was originally scheduled to be inaugurated at the same time as the new final assembly hall. However, the construction work there is a few weeks behind schedule, which is why the opening is not planned until the beginning of November. However, Schubert’s employees can already look forward to their new attractive workplace, which has been planned to meet the demands of a state-of-the-art working environment. In the future, several office areas with a flexible space system will allow agile teams to work together on a project-by-project basis. On the ground floor of the building, there are rooms for meetings and customer sessions. A flexible wall system allows conferences for up to 145 participants. The technical offices are located on the first floor, from which the technicians have a view into the adjacent new final assembly hall. The image processing and IT specialists will find their new working environment on the second floor. There is a ‘marketplace’ within the new office wing, where employees from the two upper floors can meet and interact casually. Schubert has also created a special highlight for its staff with the creation of a large, green roof terrace that can be used for breaks. Extremely meticulous planning went into the entire complex. Gerald Schubert, Shareholding Partner at Gerhard Schubert GmbH, confirms: “These work spaces are where our employees, who are absolutely decisive to our success, will be spending most of their days. This is why it is so important to us that they feel comfortable there. We have put a lot of thought into the design of the office building and the final assembly hall and hope that the new work spaces will be well received by our employees.”
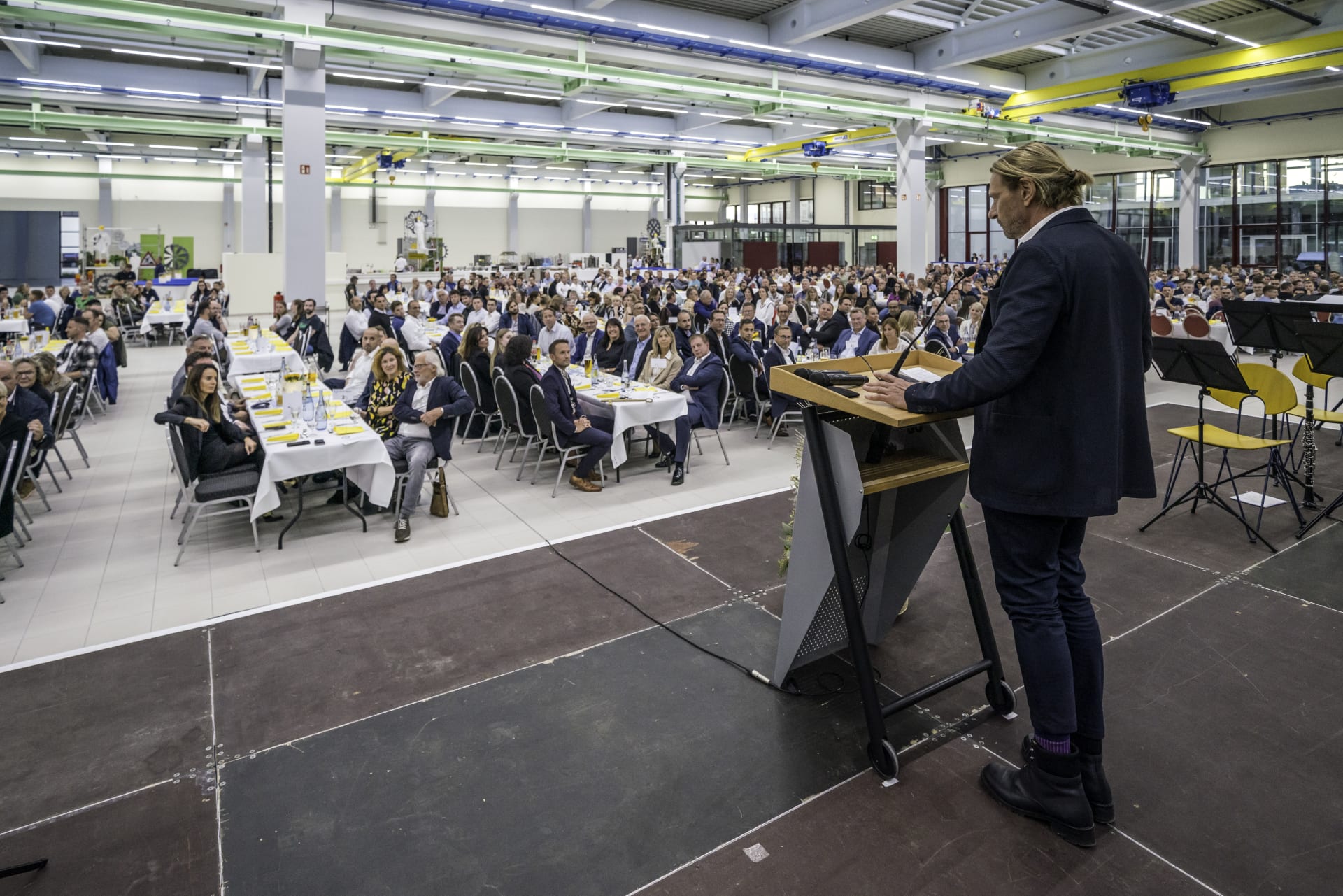
1,100 guests accepted the invitation to the festive inauguration of the new final assembly hall. Gerald Schubert provided them with details on the impressive new buildings.
Extensive preparation for the site expansion
Not only creative thinking, but also many organisational preparations were required long in advance to implement the site expansion in Crailsheim. Although the actual construction work for the final assembly Hall 3 with an office wing began in spring 2022, the road L2218 between Crailsheim and Dinkelsbühl first had to be relocated for the new buildings in 2019. This involved many discussions and coordination with the city, the regional council in Stuttgart and various interest groups of citizens, residents and environmental associations until the first specific planning steps and preliminary building applications could be made in 2017.
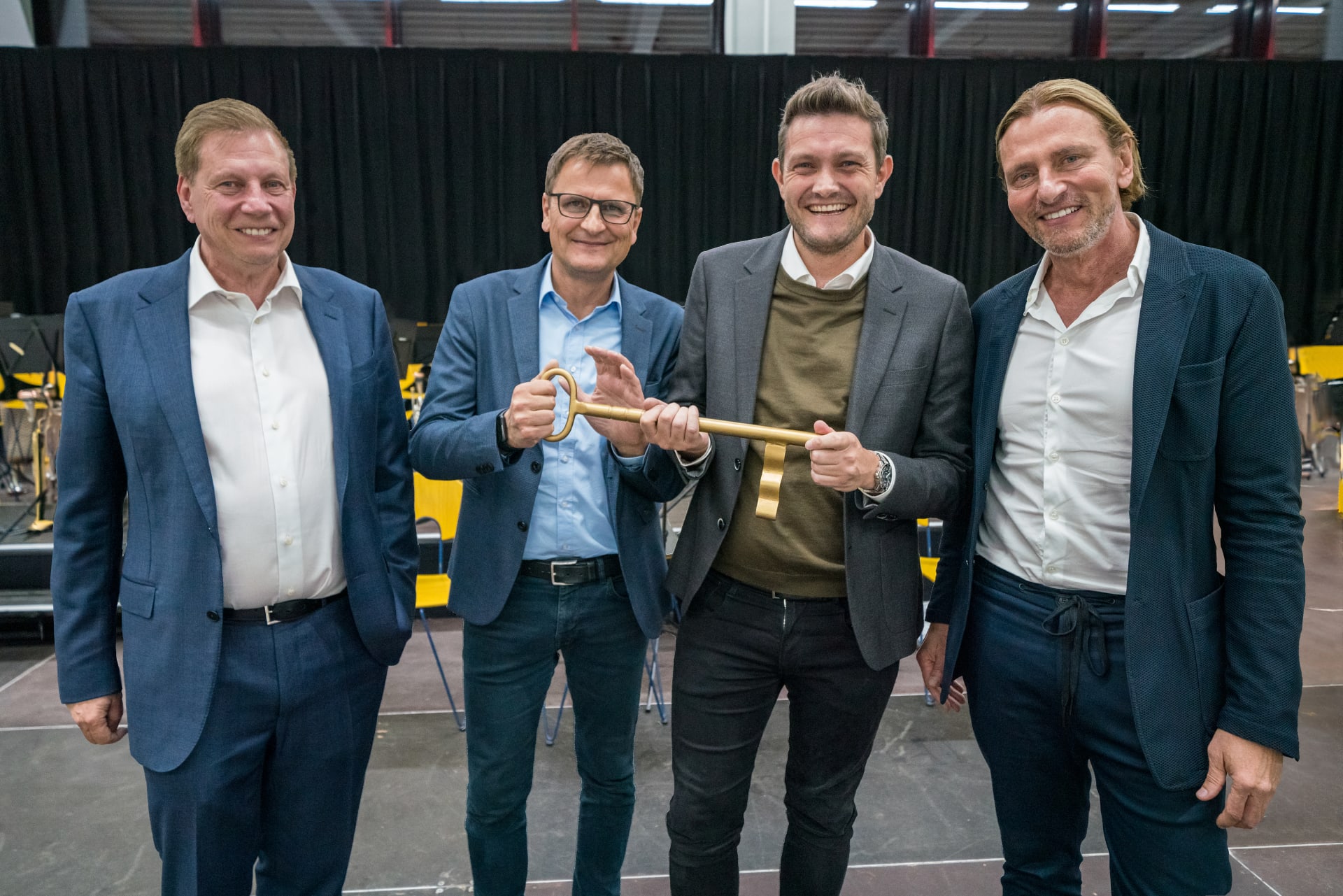
Handing over the keys: From left to right: Ralf Schubert (Managing Partner), Karl-Heinz Gaukler (Division Director Final Assembly), Marcus Schindler (Division Manager Construction), Gerald Schubert (Shareholding Partner).
A sustainable energy concept played a key role in the expansion project
The fact that environmental organisations gave the green light for Gerhard Schubert’s new building plans was in no small part due to the packaging specialist’s commitment to sustainability, as well as functionality and aesthetics, when designing its new buildings. The company aims to have CO2-neutral production and manufacturing by 2024. To achieve this ambitious goal, a sustainable energy concept was developed for the two new buildings. An underground ice storage tank is used to heat the premises. With this technology, water is continuously frozen and thawed again, whereby the resulting heat can be stored and made usable as needed. In Schubert’s case, an ice storage of 1.9 million litres of water enables the complete elimination of fossil fuels for heating and cooling. Furthermore, a photovoltaic system with 522 kilowatt peak (kWp) on the roof of the final assembly hall ensures the company’s own electricity generation, which has already been in operation since the end of August. The new photovoltaic system complements the existing system on Hall 1 North, which has been running since May this year. With both systems, Schubert can now produce more than one megawatt of electricity and cover as much as a quarter of its needs. Gerald Schubert explains: “With our Mission Blue Sustainability Initiative, we have set ourselves very ambitious environmental protection goals. We are very pleased that with our two new energy-efficient buildings we are now a step closer to achieving them.”
Tour of the final assembly hall possible on the Open House Day
The inauguration of the new final assembly hall coincided with Schubert’s Open House Day, which took place one day later on 23 September. At regular intervals, the packaging specialist invites its 1,200 employees currently working in Crailsheim to spend a day with family, friends and acquaintances on company premises. At this year’s event, as always, an attractive programme awaited the visitors. In Hall 1 North, for example, there was a demonstration of a TLM packaging system that packs biscuits. In Hall 1 South, visitors could learn more about turning, milling, lasering and 3D printing, and there were also demonstrations of the Transmodul and insights into the service department. The final assembly hall, which had been opened the day before, could also be explored. Other attractions included a pickerline for packaging pet food in action and the opportunity to get to know different areas of the administration. The wide range of information on offer was rounded off by a creative children’s programme, musical entertainment and a large selection of delicious food and beverages provided by the Hägele catering team. Visitors could also take part in a contest during their stay at Schubert, with six winners ultimately receiving a voucher for a balloon flight. Bärbel Beyhl, Assistant to the Managing Director & Marketing Manager at Schubert summed up: “Our Open House Day met with huge interest. Some 5,500 people came to find out more about our machines and the way we work. The fact that we had so many visitors is thanks to our employees, who are proud of their workplace and happy to showcase it.”