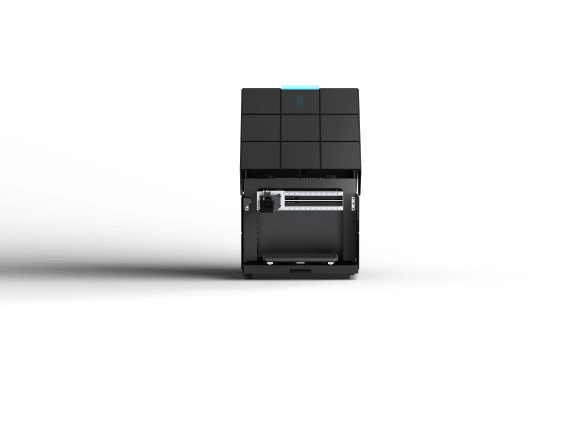
The new PARTBOX printer offers consistently high print quality, which improves process reliability within the packaging machines.
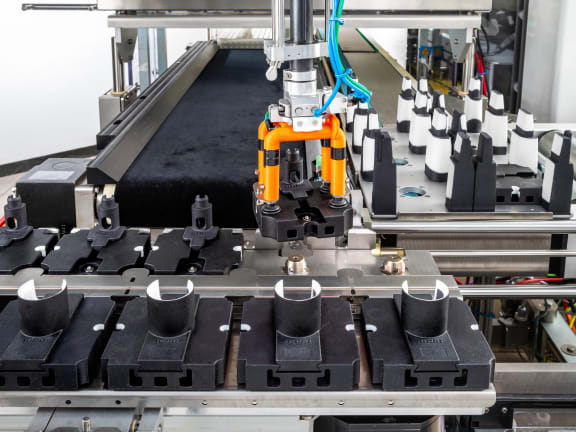
With platform and printer, the overall PARTBOX system enables components to be produced directly in the company’s own operations with the fastest possible availability.
Perfectly matched plastic material
Moreover, Schubert Additive Solutions supplies the right printing material in the form of PARTBOX Black plastic. The difference versus commercially available filaments lies in a polyamide optimised for the FDM (Fused Deposition Modelling) printing process. The material is food-grade and detectable with a metal detector. PARTBOX Black also features excellent mechanical properties and high temperature resistance. This allows very smooth surfaces to be achieved in the printing process. Hardware, software and material are therefore perfectly aligned. The new printer is easily connected to the Internet via the LTE standard. As an additional highlight to this overall package, the new 3D printer was also developed by the Ottenwälder und Ottenwälder design agency. Their collaboration with Schubert in product design spans many years and yet again ran very smoothly this time, as Conrad Zanzinger confirms: “We are very pleased with the result!”
With its own streaming platform and printer, Schubert’s PARTBOX is now a complete system that enables manufacturers to produce components directly in their own operations – with the fastest possible availability. The digital process saves customers processing, shipping and warehousing costs. Delivery of the new printer will begin in April 2022 after the Anuga trade fair.