Over the last decades, fast-moving consumer goods have significantly contributed to the evolution of automated packaging processes. The TLM packaging machines from Schubert, with their flexibility and high degree of automation, have been instrumental to these advances. The ability to make quick format changes for frequently changing products gives manufacturers a highly versatile all-rounder packaging system with which they can quickly react to changing markets while setting trends in product formats.
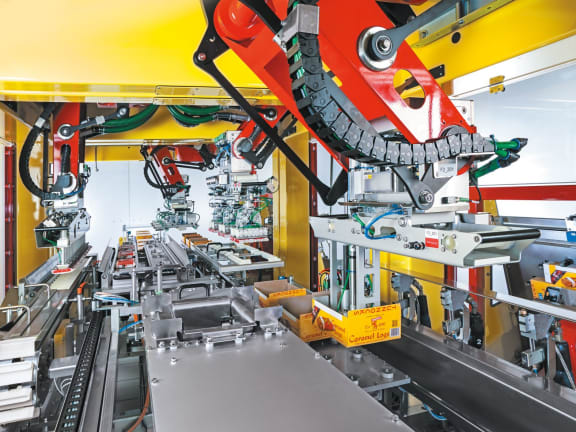
Tunnock’s, the British confectioner, uses TLM systems to package chocolate wafer bars.
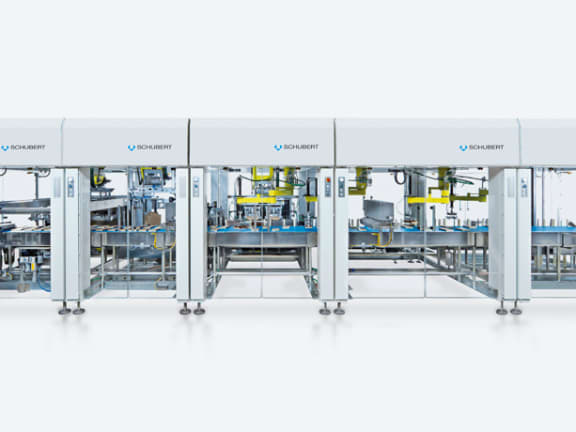
With the modular top-loading machines from Schubert, if the customer requires higher-level performance, all it takes is the addition of a further submachine.
A sustainable investment
A packaging machine also has to ensure that quality is reproducible – at any time and around the clock. “Especially for fast-moving products, packaging machines should be designed so that they can perform and produce in three shifts. Only then will they pay for themselves quickly and only then can the customer achieve profitability with a new system,” says Ralf Schubert. Boyd Tunnock – a Scottish icon, a successful confectioner and long-standing Schubert customer – got straight to the point in an interview with Packaging News magazine: “You only get what you pay for.” It is no secret that the value of a system is closely linked to its purchase price. “With the wafer bar packer from Schubert, we have a high-quality TLM machine that is especially sustainable thanks to its exceptional flexibility. It is very important to us that an investment be sustainable,” says Boyd Tunnock.
Reduced to the best
There are many opportunities to profitably tap the potential of the TLM machines. “We make our machines simpler, more accessible and more flexible. We reduce conversion times, offer fully automatic equipment changeovers and eliminate unnecessary interfaces between individual sub-processes,” explains Ralf Schubert. The basis for these developments is the reduction of mechanical parts and increasingly intelligent control. Since the software does not wear out or require maintenance, this technology proves to be not only flexible, but also cost-effective in operation.
Whittaker, the Australian chocolatier, experienced this over three decades ago. Brian and Andrew Whittaker still have a special place in their hearts for their very first Schubert system, a 1982 SSB/SKA. Today, it is still in daily operation boxing 13 to 15 million chocolate bars annually. With their most recent TLM picker line, over and above the system’s high line efficiency, Brian and Andrew Whittaker enjoy the added certainty of having made a purchase they will capitalise on over several decades.
“The efficiency and flexibility of our systems over their entire lifecycle allows producers of FMCGs to continue to produce very competitively even in high-income countries,” says Ralf Schubert. “We are proud that we can contribute to their success with our systems.”