Packaging machines with the modular image processing system
The pick & place vision system ensures consistently high quality
Automation is inconceivable without industrial image processing. Image processing systems also play a major role in automated packaging processes. This is by no means insignificant, because an essential feature of processes such as pick & place or flow-wrapping machines is the continuous flow of product. Cameras, however, work with individual images that cannot fully represent the product flow. This is why Schubert developed its own pick & place vision system, which is tailored to the requirements of packaging machines and supports the use of robotics.
A vision system for quality control
With its pick & place vision system, Schubert customers primarily benefit from automated and highly efficient quality control: Only products that meet the customer’s programmed specifications are recognised by the vision system and then picked up by the packaging machine’s pick & place robots. Whether a flow-wrapping machine, a case packer or simply pick & place – at the end of the packaging process, the manufacturer benefits from fewer rejects, fewer complaints, lower costs and a guarantee of consistently high product quality.
Modular imaging systems for every application
Line sensors are a fundamental component of Schubert’s pick & place vision system. They are integrated into the incident-light scanners and 3D scanners, and enable a continuous product flow to be observed. Like all system components in Schubert packaging machines, the vision system is also modular in design: The 200-millimetre-wide modules can be combined in one scanner up to a working width and therefore a product width of 1800 millimetres. To complete the industrial image processing, the vision system also includes integrated lighting, software and other applications. These include the “reach into the box” feature, where products are picked up from the pile by a robot in pick & place.
The future: Neuronal networks
There are, however, products which cannot be inspected with conventional image processing. This is because classic pick & place vision systems are based on the fact that products can be clearly identified with just a few parameters. In the case of so-called “living” products, which have high production tolerances, the deviations are so great that they are difficult or impossible to describe mathematically. The software would have to check too many parameters, which are also correlated and interdependent. This is why Schubert will rely on neuronal networks and artificial intelligence (AI) for its vision system in the future. The image processing system therefore learns on its own and sorts the products into classes independently in a longer learning process. This means that the parameters are selected by the system and no longer by the programmer. For customers, this means a significant step towards independence: In the future, they could actually use neuronal networks, under certain conditions, to teach their packaging machine to handle a new product on its own.
Modular scanner technology
Image processing with a vision system in 2D and 3D
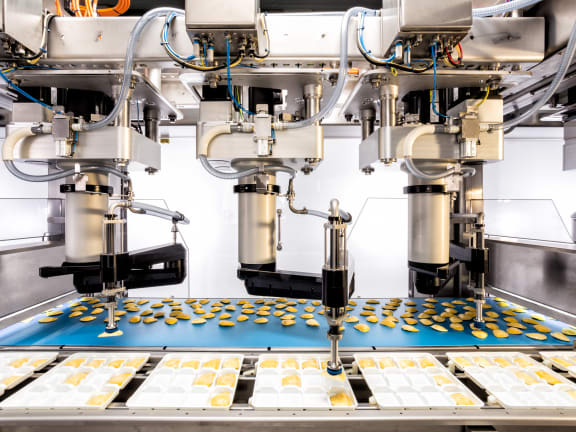
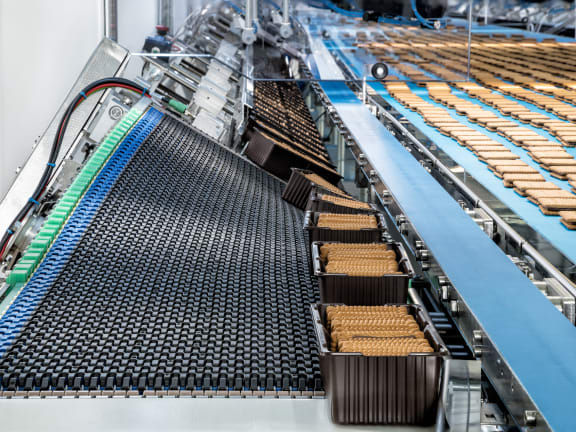
Quality control in practice
Pick & place with the vision system
The modularly designed pick & place vision system
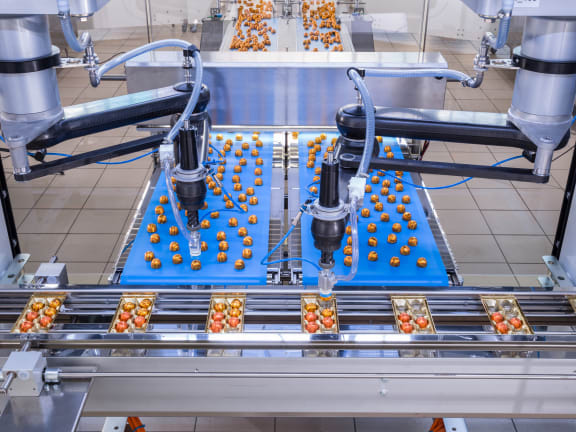
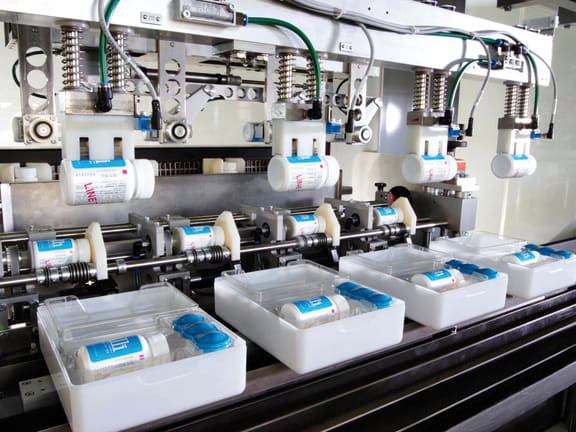
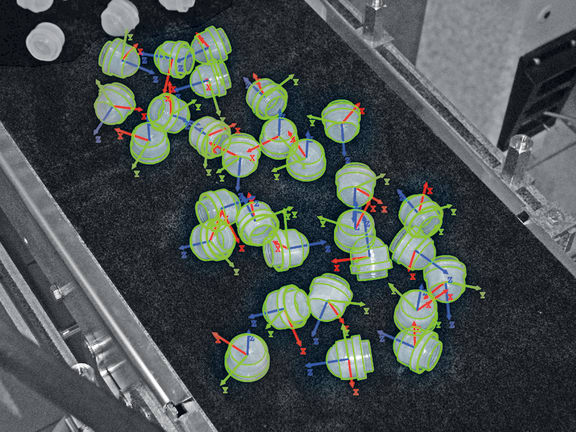
Contact
Would you like further information?
Ask our expert!
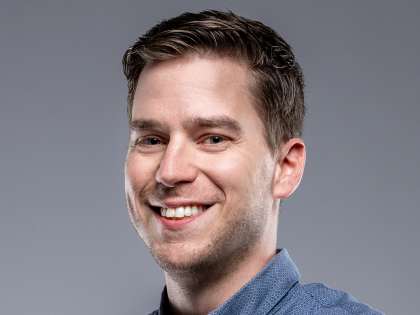