Today, no food manufacturer can afford to ignore the market’s need for rapidly changing, individually tailored packaging solutions that also conserve resources. The latter is a special challenge in the case of packaging into flowpacks. There is a good reason why composite films have conquered the world thanks to their ease of processing and product-protecting properties. However, the shift towards materials that are more recyclable will become increasingly pronounced and is likely to be irreversible in the long term. The answer to these developments is flexibility. Companies that can change their packaging processes quickly and as needed gain a competitive edge in the marketplace, especially when it comes to environmentally conscious consumers and future trends. With the Flowpacker flow-wrapping machine from Schubert, manufacturers of almost any product can capitalise on a packaging machine that combines effective packaging solutions with extremely variable processes – thanks to its modular design and the use of highly developed robot technology.
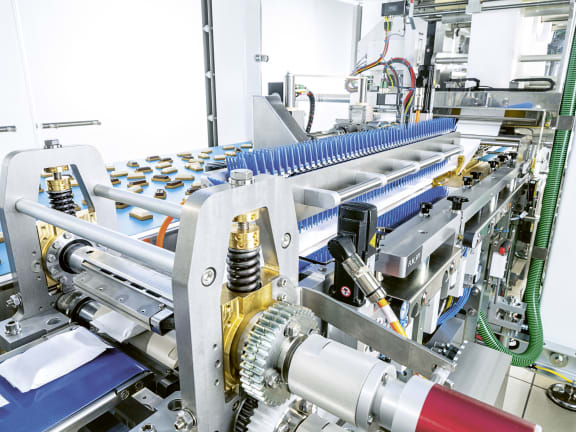
With the state-of-the-art sealing technologies, both conventional and sustainable flow-wrapping films can be used in the same line.
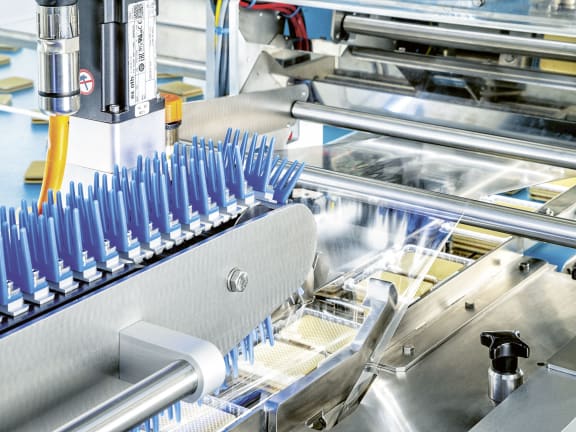
Both plastic trays and trays or boards made of cardboard can be processed in the bakery's flowpacker machine.
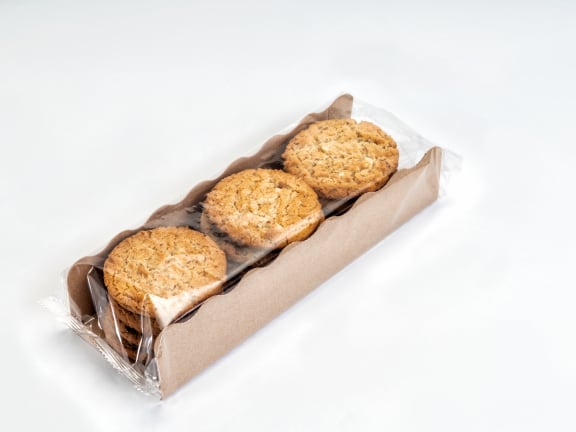
A long-established bakery in Alsace packs its biscuits and pastries with recyclable packaging materials using Schubert’s flow-wrapping machine.
High processing quality and excellent machine efficiency
The exceptional flexibility in terms of product specifications and packaging material is one thing about the Schubert flow-wrapping machine, and the high processing quality and machine efficiency are another: Thanks to the robot-assisted processes, especially sensitive products such as Alsatian pastries, are packaged extremely gently. Long conveyor belts are superfluous. Instead, F4 robots place the biscuits flexibly and gently into the trays or directly into the chain. Breakage, damage and rejects are therefore minimised. Moreover, the Schubert image processing system inspects the goods in each Flowpacker to ensure that they are in perfect condition. Only products that meet the specified quality criteria are picked up and packed by the pick & place robots. At the bakery, an incident-light scanner is used for this purpose. Depending on the requirements, however, 3D image processing can also be used in the flow-wrapping machine, and for example, record and assess the product height.
With the flow-wrapping machine, manufacturers in the food industry in particular can benefit from highly flexible and reliable packaging processes: The wide range of options in the choice of packaging, the products to be packaged and the options on recyclable materials make the Flowpacker a future-proof packaging machine which can accommodate the fast-moving food industry in every respect.