With the new Box Motion unit, Schubert now provides its customers with even more flexibility and the highest quality when sealing flowpacks in the flowpacker. The new technology for cross-sealing is designed in such a way that the fixed sealing jaws clamp the film completely at the sealing seam and seal it ultrasonically, while the unit moves linearly during the sealing process in accordance with the film speed. Stefan Horvath, Product Manager at Schubert, explains: “The time during which the Box Motion unit moves with the product and film is equivalent to the sealing time. This can be set to a constant value, depending on the film speed – as is also the case, incidentally, with our conventional, rotating and flying cross-sealing unit with the heat-sealing process. The fact that manufacturers can set a constant sealing time is very important to ensure consistent quality in the packaging process.”
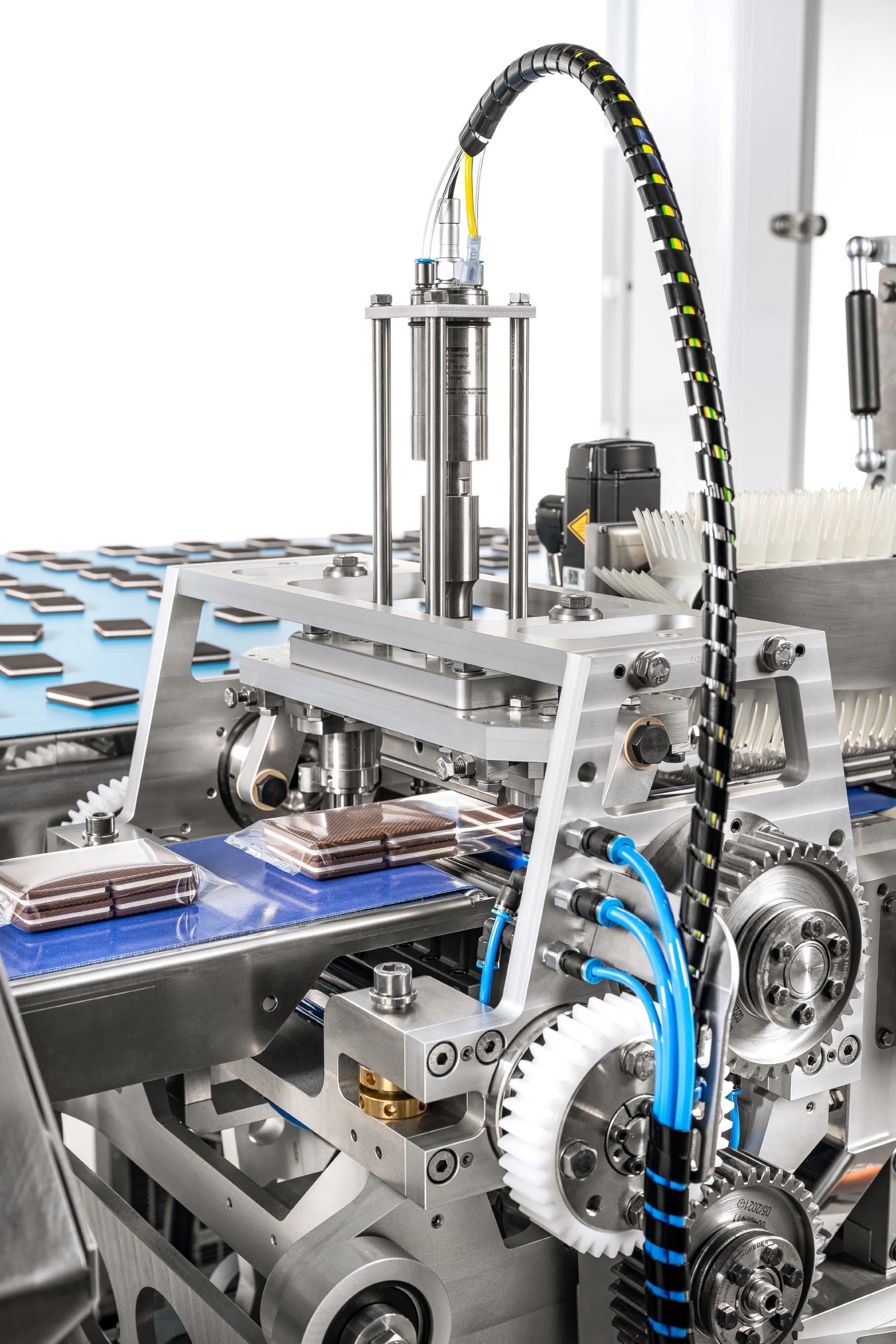
The Box Motion unit is a format part that can be removed in just a few steps and exchanged, for example, with a rotating flying cross-sealing unit for heat sealing.
Advantages of the Box Motion process: Tighter sealing seam, broader selection of films
But it isn’t only the constant sealing time that contributes to quality. With the help of the Box Motion process, it is possible to seal more hermetically overall, because the sealing seam has a consistently high quality across its entire width. Products that have to be packaged in a modified atmosphere are therefore sealed especially securely with Box Motion. Thick films that require longer sealing times can also be processed without any problems. The ultrasonic process used in the Box Motion unit is ideally suited for recyclable flowpacks made of monofilms or paper-based films. “The ultrasonic process is also very clean and easy to maintain,” adds Stefan Horvath. “So the cleaning required for machine parts is much less than with conventional heat-sealing processes.”
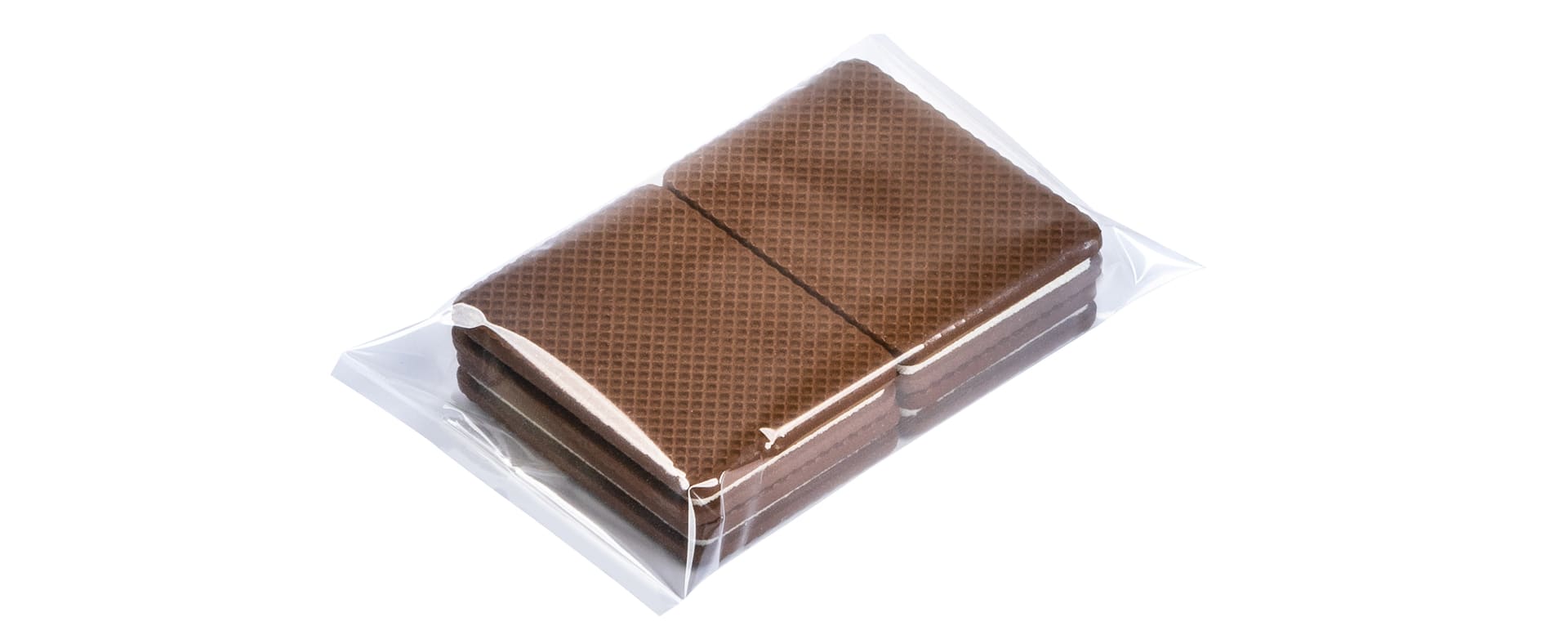
The new cross-sealing with Box Motion is also suitable for products with higher demands on sealing seam quality.
Flexible technology, easy retrofitting, high degree of future-proofing
The new Box Motion unit is a format part that is very easy to change. The unit can be removed in just a few steps and exchanged, for example, with a rotating flying cross-sealing unit for heat sealing. Conversely, the Box Motion unit can be quickly reinserted via plug & play. Effortless switching between a rotating and a Box Motion system offers manufacturers the greatest possible flexibility and increased future-proofing, as it is possible to respond quickly to new market requirements. Stefan Horvath explains: “Our customers often need flowpack films with different thicknesses and barrier properties for their products. Now they can easily switch back and forth between the cross-sealing technologies. If manufacturers want to use a Box Motion unit on their flowpacker at a later date, for example because they want to switch to more environmentally friendly films, they can simply retrofit it.”
With the expansion of Schubert’s cross-sealing portfolio, customers now have freedom of choice in terms of product, packaging material and sealing technology, and can effectively position themselves to meet the packaging needs of the future.