Not an option, but a must – manufacturing companies that still want to thrive in the market in a few years’ time can no longer afford to ignore digitalisation. However, the Industry 4.0 revolution is making considerable demands on businesses, ranging from major investments and the creation of new processes to extensive workforce training. Especially in the fiercely competitive and fast-moving consumer business, it is important for manufacturers of food, confectionery, cosmetics, and beverages to keep pace with digital developments. It is the only way to maintain competitiveness in the long term. In the increasingly stringent framework of high energy prices and strict climate protection requirements based on the Green Deal, it is well worth exploring the opportunities of digitalised production and the IIoT (Industrial Internet of Things) anew. In the future, the challenge will be to produce not only cost-effectively, but also more sustainably in a European context with comparatively high wages and a shrinking skilled workforce.
The key to more sustainability and efficiency
The more efficiently a production line runs, the less waste there is when it comes to raw materials, products and ready-to-sell packaging – and the more sustainable the entire manufacturing process of an FMCG manufacturer will become. It enables companies to improve their carbon footprint and is well received by consumers. Two key factors need to be considered to successfully manage radically changing requirements: Automation and digitalisation. And yes, both play hand in hand. Efficiency and sustainability are most likely to be achieved through automated processes that can be continuously monitored digitally and adjusted or improved as needed. Especially with the food sector’s large product volumes and highly perishable goods, every unplanned machine stop instantly results in product rejects and higher costs, including the ecologically questionable topic of wasted food. The ambitious goal for producers should therefore be to achieve flawless production without unplanned stops and rejects. This is difficult to achieve without a precise analysis of possible weak points, identified long before any unplanned stop. And this is exactly where digitalisation comes in.
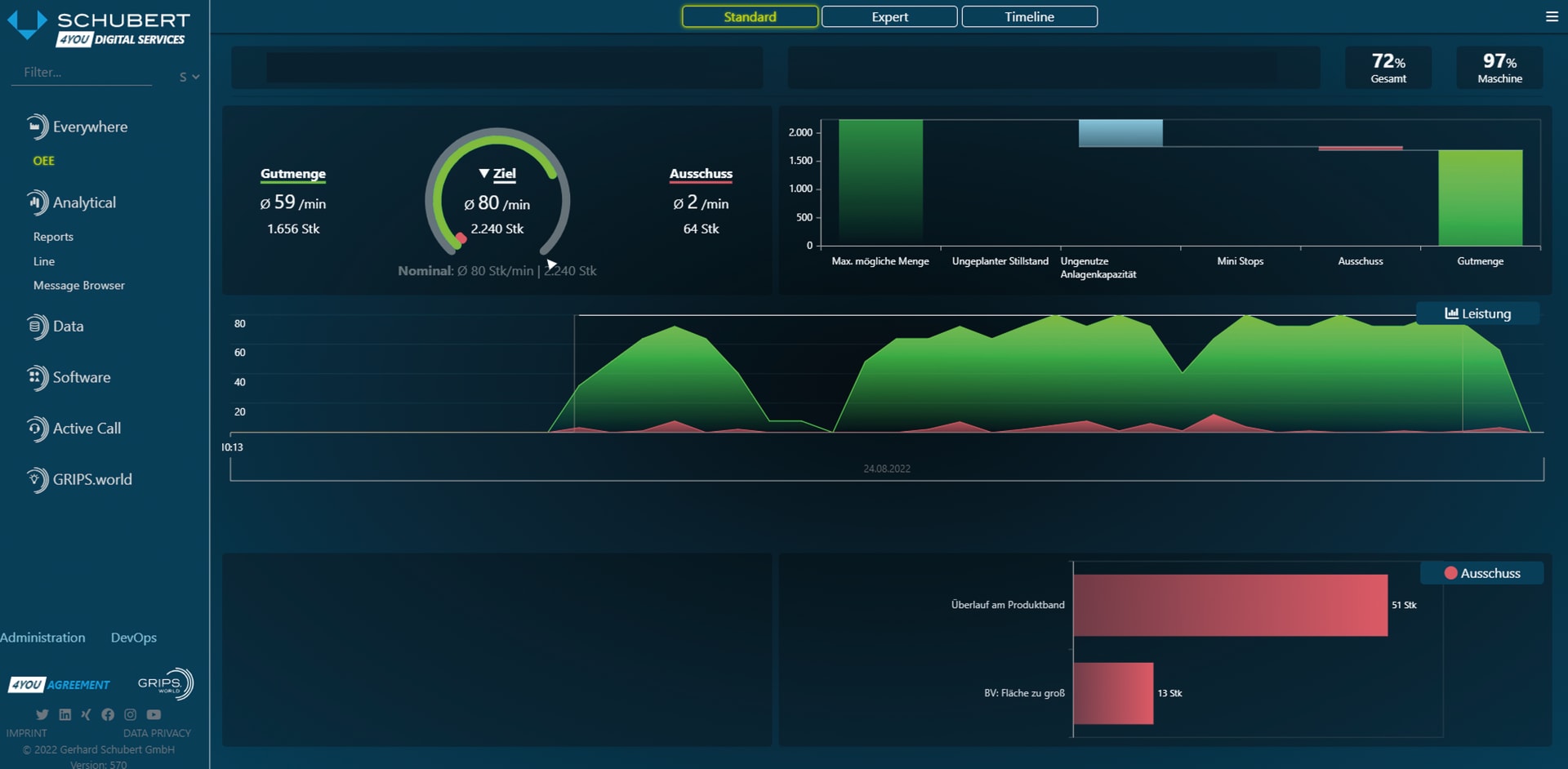
The data evaluation of Schubert machines on the customer portal is currently being optimised for even better user-friendliness.
Tremendous potential for more efficiency
The masses of data generated in modern production lines represent a virtual gold mine that can be exploited with the right expertise. Data evaluation at various levels makes every machine transparent: It provides valuable input for optimising existing processes, useful information on when and which maintenance of individual machine components should take place, or even initial error messages that indicate an impending problem. The key is to select the important data from the multitude of individual raw data – such as the temperature sensor on a robot motor or the error message on a glue nozzle – to then condense it and draw the right conclusions.Big Data is the starting point, but it is the fine-tuning that brings the desired results and an increase in efficiency, quality and sustainability. There are numerous unexploited and perhaps even unimagined opportunities for manufacturers to make their production more cost-effective and ready to take on new challenges.
Identifying and clearing obstacles
One of the most frequent topics of discussion in industry is the analysis of machine data. It is, in fact, something that promises manufacturers many advantages – if only it weren’t for the unresolved issues of data protection and legal certainty between machine operators and machine manufacturers. Who owns which data? Who is allowed to store it, evaluate it, or even pass it on, and how? So far there are no standards for all of this. In principle, a contract or licence has to be concluded between the partners for each individual case. The “Guidelines for Data Use” defined by the VDMA (German Engineering Federation), which includes not only German but also other European companies, provides some guidance. Ultimately, however, a high degree of trust is needed between the business partners, all the more so when it comes to the sensitive issue of monitoring competition.
There is also a second obstacle which has very different implications depending on the company: Digitalisation and data use cannot be achieved without a company’s IT department. As diverse as individual manufacturers are, so too are their IT architecture, network structures and corresponding IT policy – which sets rules for the use of all hardware and software, including data processing, for employees. All in all, this is an extremely complex field that requires a great deal of expertise and on which the main responsibility for data security hinges. The trade-off between protection and progress at this point is a difficult balancing act for all parties involved, including managing directors, IT experts, skilled workers and machine operators from production.
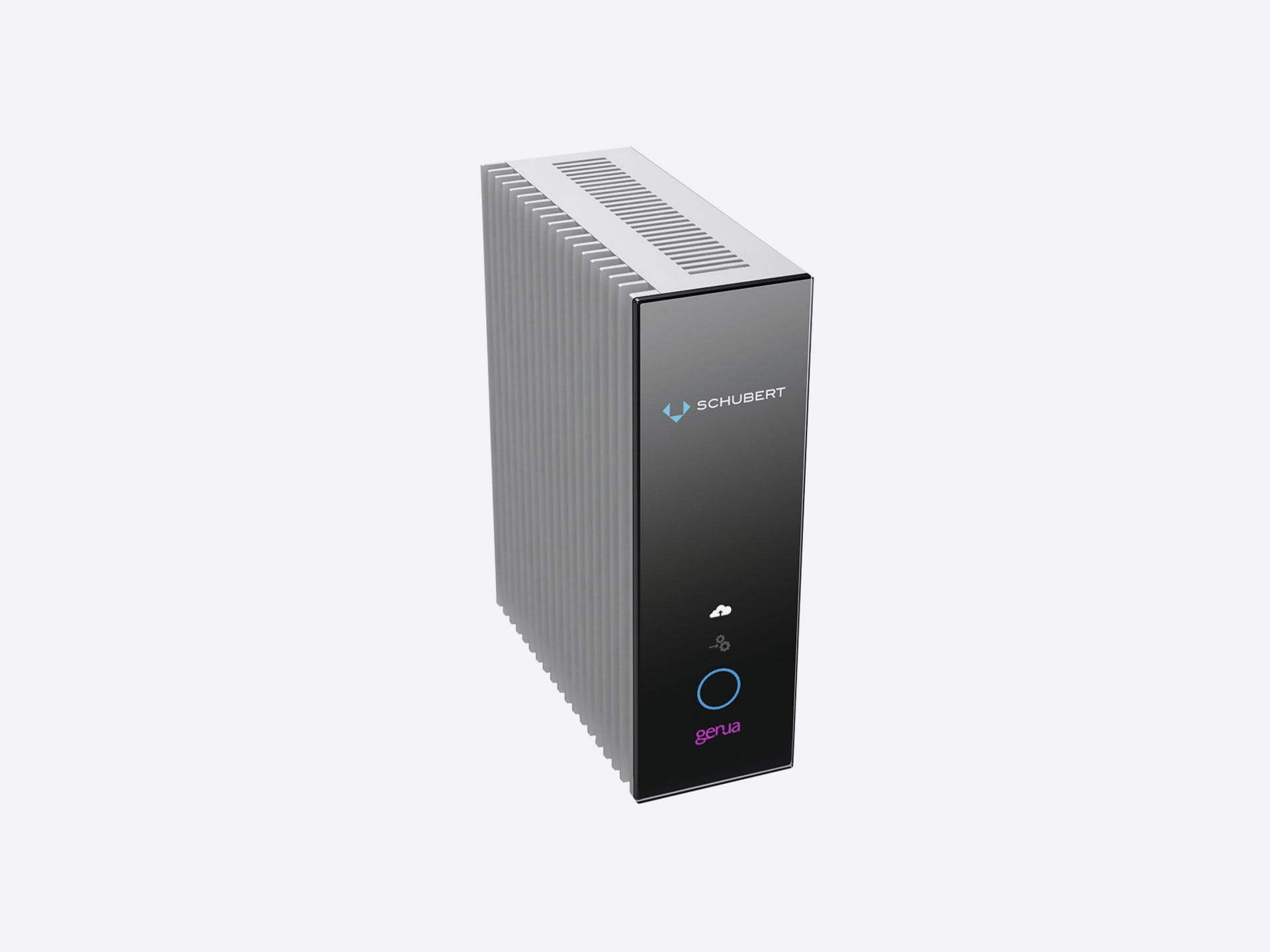
The gateway, jointly developed by Schubert System Elektronik and genua, meets state-of-the-art IT security requirements by keeping customer networks and the internet separate.
The issue of data security
Schubert, the packaging machine manufacturer, has experienced this directly. And it offers its customers the possibility to evaluate the raw data of Schubert machines specifically for them, for example to eliminate faults more quickly, introduce preventive maintenance or increase a packaging machine’s performance. This takes place via a customer portal in which the data is collected and presented in different analyses with varying levels of detail. Operators therefore have to decide whether to grant Schubert access to the customer portal via the internet to benefit from the services. Uwe Galm, Director of Customer Services at Gerhard Schubert GmbH, reports: “The decision for or against our digital CARE Services is often determined by the various interests within a company, the existing IT architecture and the IT policy. We often see that investments in digitalisation have already been made. However, it is often not possible, especially for medium-sized businesses, to build up the necessary expertise to enable strategically meaningful data analysis in-house – quite simply due to the demanding nature of the subject matter. Our service experts can close this gap.”
Uwe Galm understands that the human factor should not be underestimated: “Our customers’ concerns are extremely important to us and are always an incentive to do better. This is why our GS.Gate industrial gateway, which we co-developed, is installed in all new Schubert machines. It meets the latest IT security requirements by separating customer networks from the internet. The machine data is collected on the gateway similarly to edge computing and displayed in the customer portal on request. By the way, we are currently revising the presentation of this data in the portal itself together with some of our customers to make it even more user-friendly.” Schubert only gains access to the portal from the outside if the customer agrees. Uwe Galm adds: “During access, the security of the customer network is always ensured by the GS.Gate’s unique architecture.”
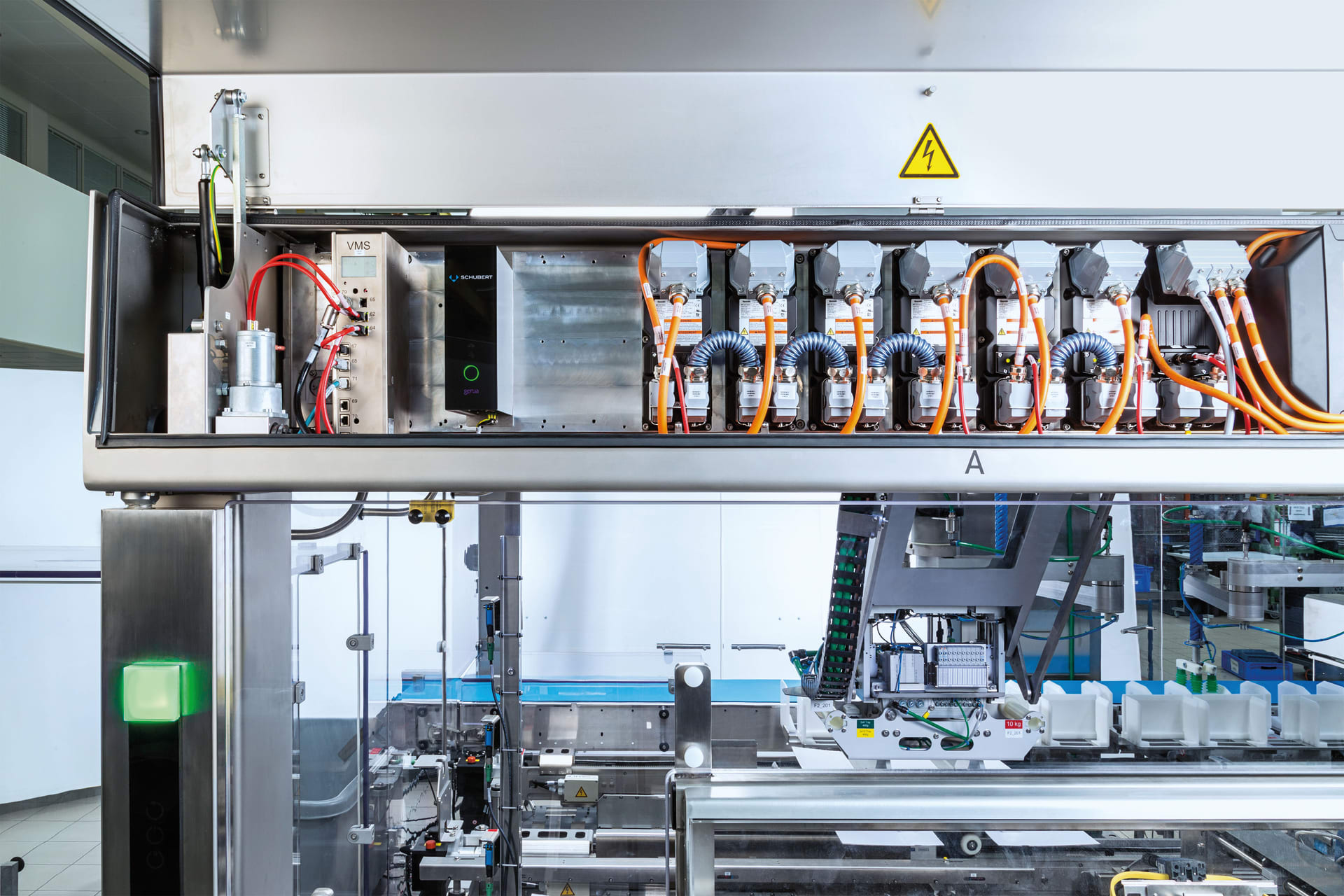
All new Schubert machines are equipped with the GS.Gate industrial gateway. The machine data is collected on the gateway in a manner similar to edge computing and displayed in the customer portal on request.
Added value in practice
Schubert considers it very important to position its customers to successfully meet the challenges of the future. “For us, this most definitely includes making use of new digital technologies. Above all, we have to explain to our customers the added value these advances can generate,” highlights Uwe Galm. This is why the machine manufacturer not only offers a test stand with clearly illustrated real machine examples, but also free use of the customer portal for 30 days. For some companies, the digital services are already yielding visible successes. For example, the customer portal quickly put the Schubert experts on the right track when troubleshooting a customer’s line, and food manufacturer Kühne was able to significantly increase the performance of its line together with Schubert through OEE analyses.