Schubert North America has emphasized the importance of operator and technician trainings early on. When establishing it’s regional North American headquarters in Charlotte, North Carolina, in 2015, the company opened up a training center for North American customers. Equipped with two training machines and a classroom style meeting room, the training center has been an important component of Schubert’s successful growth strategy on the North American market.
By acquiring 7.36 acres in 2022 to build an even bigger facility with a production hall and a much larger center for spare parts management and training, Schubert has started accelerating it’s North American customer service to an excellent level.
During the following interview, Valentin Wolf, Project Manager of Customer Trainings at Schubert North America, shares his insights and his vision about Schubert’s North American customer training portfolio.
How many trainings do you offer per month and why do Schubert’s customers need trainings on the machines?
We offer about two seminars a month. The key to efficient production is the right interaction between human and machine. Our goal is to provide training to our customers that helps them maximize machine efficiency and minimize downtime.
How many trainings does a customer typically require per year?
The number of trainings per year depends on the customer’s turnover and the number of machines they have installed at their facility.
How do you ensure to offer the right training to each customer?
We tailor our trainings towards our customers. We offer two different levels of seminars at our Charlotte training facility: VMS Level 1 and VMS Level 2. In addition to our training seminars, we offer onsite Operator training, mechanical machine and electrical machine overview trainings as well as a number of specialized on site trainings. Recently we’ve also started to partner with Bihl+Wiedeman for „AS-i Trainings“.
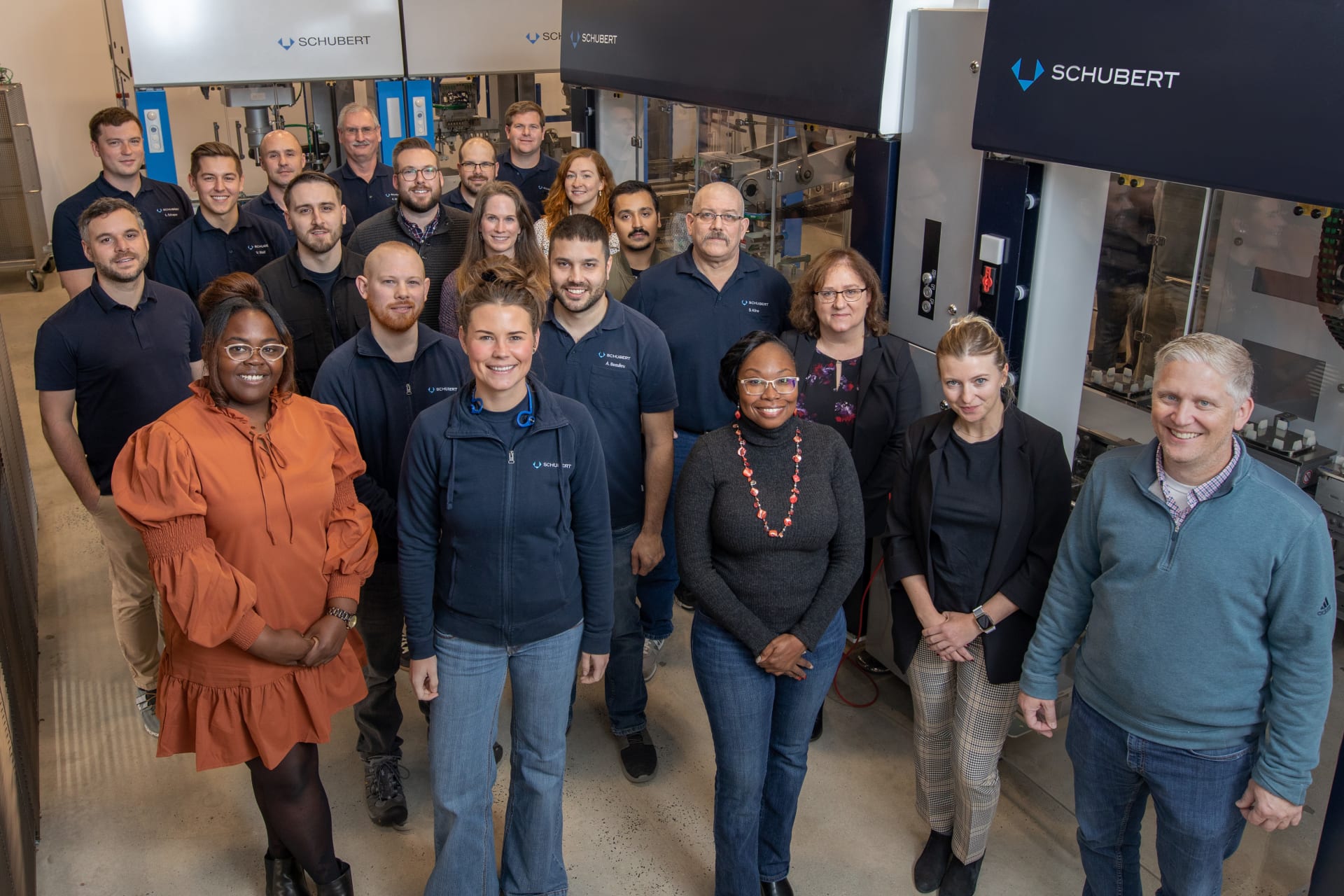
The Service Team at Schubert North America is ready to support customers
What’s the Schubert advantage?
The biggest advantage is our modular construction principle. Our machines consist of a number of standard robots which are built in-house. Once our customers are trained on these standard applications, they can apply the learned knowledge to any other Schubert machine. In our Charlotte training center, we have two packaging machines with most of our standard applications installed. During the training seminars, we can replace components, modify the program and simulate faults which is for the most part not possible at a customer’s site.
Our VMS (Packaging Machine Control) is a custom-made control system for Schubert Packaging machines. The software has many built-in tools that help our customers troubleshoot potential faults or make changes to increase machine efficiency. Changing robot movements, tracking faults, troubleshooting bus systems, or creating a new recipe, all can be done with one control software.
What’s your vision for the future?
The goal is to increase the training capacity and expand the training portfolio for our North American customers to better meet their needs. Our customers‘ positive feedback shows we’re on the right course, our customers like the mix of hands-on and theoretical content in the classes at our Schubert training center.
About Valentin Wolf
Valentin Wolf has been with Schubert for more than 11 years. His extensive experience in mechanical and electrical engineering, gained during his early career as field service technician, at Schubert in Europe and in North America puts him in an ideal position to offer our customers the best machine operator training possible. His technical knowledge helps him understanding our customer’s requirements and questions. Since he has worked with many of Schubert’s North American customers in the past, he has a great understanding of their processes and the challenges they face in their day-to-day operations. Together with our entire team of trainers, Valentin strives to continuously improve the Schubert customer experience in North America.