Klaus Pelzer began his career at Gerhard Schubert in 1986 as an electrician. Once he completed his training as an electrical engineer in the 1990ies, he was amongst others responsible for putting customer systems into operation. Given his expertise, he was quickly recognised and valued as a highly competent troubleshooter.
Initially, he was able to handle the telephone inquiries himself along with his other responsibilities, but soon there were so many Schubert machines in use that managing the telephone customer service was a full-time position. The hotline was therefore established in 1994 with Klaus Pelzer as its first employee. The department now includes a staff of four.
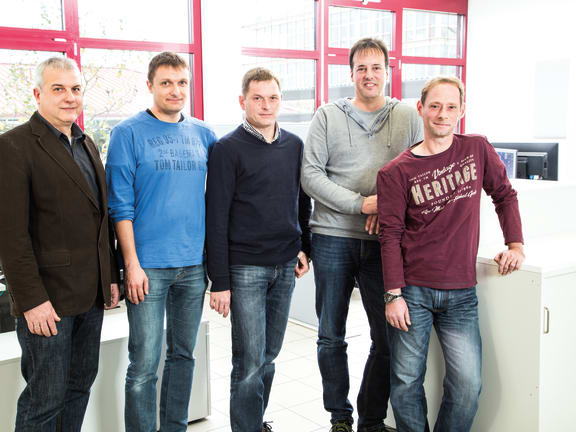
Klaus Pelzer’s team solves more than 90% of the issues on the phone or via email.
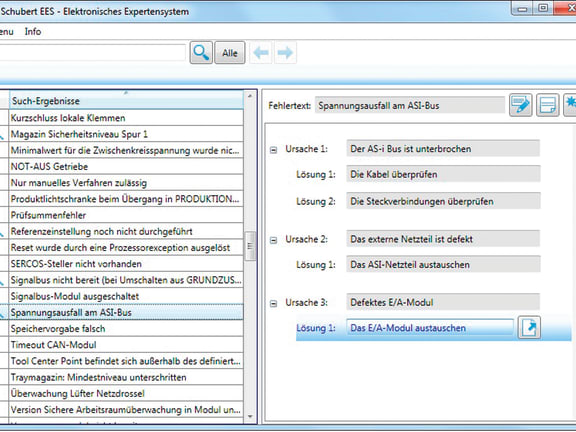
All hotline cases and their solutions are saved in the elcetronic expert system (EES).
Specialists on the phone
Klaus Pelzer doesn’t rely solely on the database. For unusual emergencies, he has all the documentation for older systems on hand. “Just recently, a large customer called who was still using a 1988 SNC F2 to pack small colourful chocolate candies,” says Pelzer. “This isn’t an exception. Many of our machines have been in use for 30 years and even longer. So it’s important for all of us to be familiar with our ‘classics’ as well.”
To stay up to date, the specialists make it a point to find out what is currently going on in product development. The hotline offices are located close to production and the development department. “The short distance to production is very convenient. We can even bring our phone to the machine and try out what works best,” says Pelzer. “As well, the technician can come into the hotline office and provide advice when issues arise.”
Schubert’s hotline department doesn’t staff telephone operators, but rather specialists who are fully integrated to the company and who have extensive expertise. Customers aren’t the only ones who appreciate and value this expertise. Employees from all departments don’t hesitate to contact the hotline when they have questions.