As a forerunner in innovative technology, Schubert is taking advantage of changing conditions to further expand the digital capabilities it has developed in house and that are already available in its modular packaging machines. In doing so, the company can leverage a very significant advantage. This is because Schubert’s long-established philosophy of integrated, interface-free packaging machines has led to a steady growth in in-house expertise and to an extraordinary vertical range of manufacture – also at the digital level. The unique combination of expertise and digital data is the currency upon which Schubert will be generating new, proactive services for mobile maintenance. After all, machine availability is always a top priority. During the lockdown, for example, the packaging machine manufacturer not only carried out virtual commissioning of its packaging machines, it also provided such skilful support to a customer in Asia via the Internet that they were able to assemble and commission their new system independently on site – without a single Schubert technician actually being present.

With the GS.Gate from Schubert subsidiary Schubert System Elektronik, an industrial gateway is now built into every Schubert packaging machine ex works.
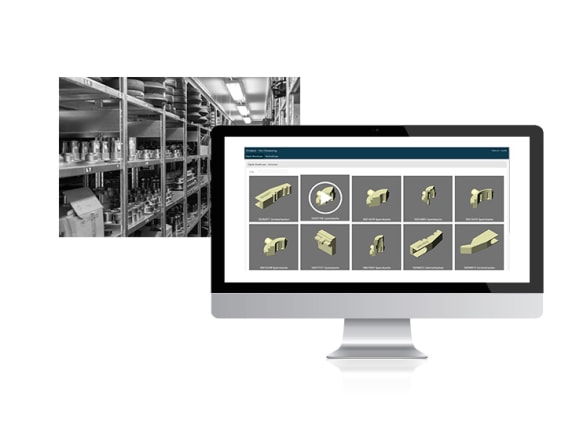
With the new PARTBOX part streaming platform, Schubert will be making certified digital print jobs available to its customers in the future via the Internet.
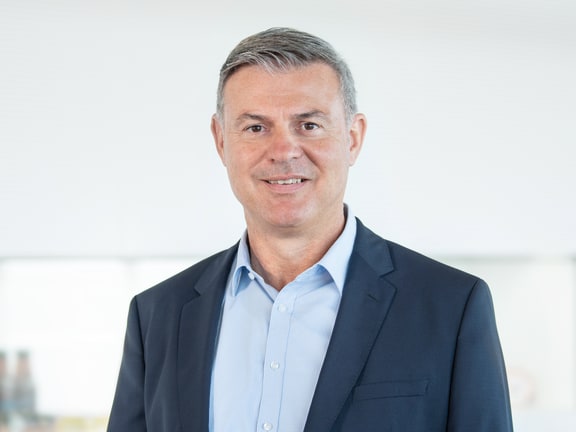
Uwe Galm joined Schubert in April 2020 as Director Customer Services.