The Flowpacker – the film expert
Sustainable films for a new packaging world
The world of films is in upheaval. As a result of stricter laws and social developments, the sustainability of materials for packaging in flowpacks is becoming increasingly important. There is no doubt that the future belongs to recyclable and compostable films. In order to remain competitive, manufacturers must adapt to this market trend on a permanent basis. This works best with a highly flexible flow-wrapping machine that can easily process a wide variety of films – not only plastic, but also paper-based.
This is more complex than it may appear at first glance, because the composite films used so far have numerous properties that are absolutely necessary for protecting the products and for automated packaging. Only very flexible, tear-resistant and easily sealable materials are suitable for use in a flow-wrapping machine. Additionally, the packaged goods must be protected from external influences by barrier layers in the film. Otherwise, durability and product quality cannot be sufficiently guaranteed.
The industry is still relatively in its infancy regarding the development of new materials. Currently, mono films made of plastic and the first paper-based films are being used. This is not possible with every packaging machine. But there is one that can already keep up: the Flowpacker! The flow-wrapping machine from Schubert packs with all three variants, i.e. composite films, mono films and paper-based films.
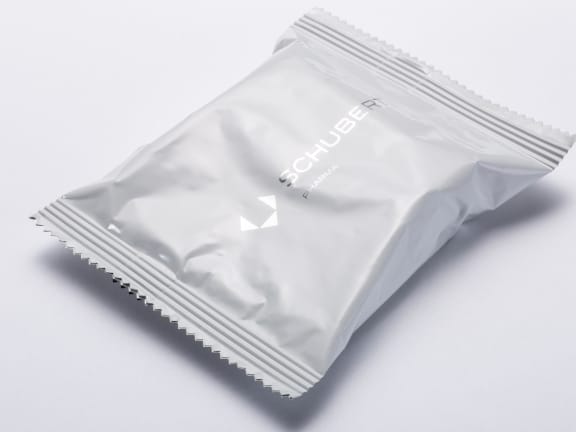
Benefits of the Flowpacker
Free selection from the entire range of films
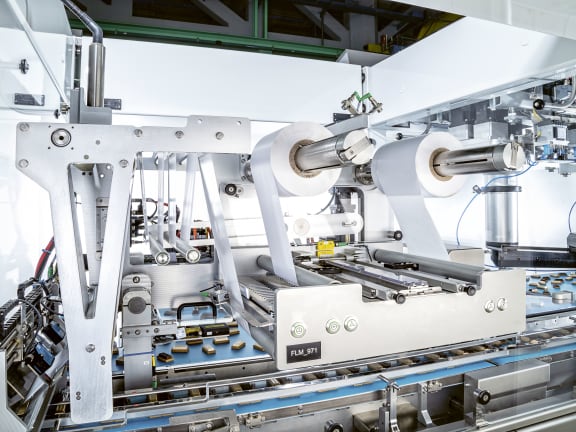
A double technological advantage in the flow-wrapping machine
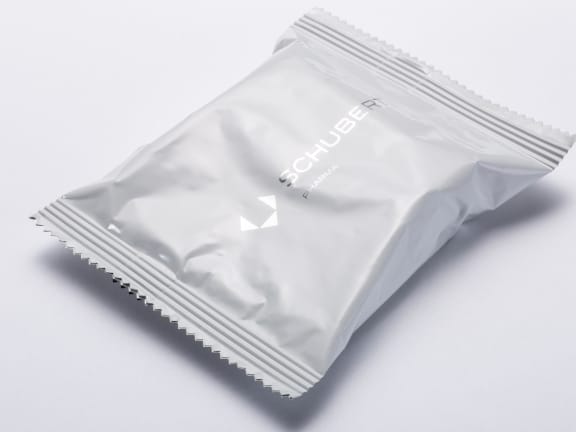
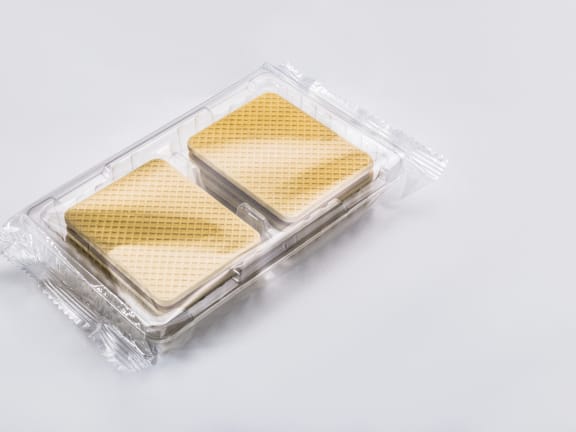
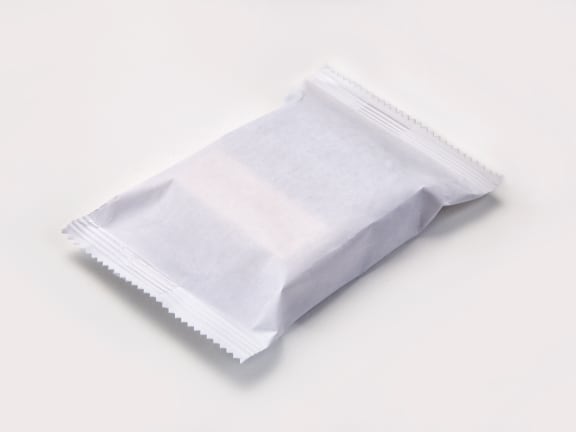
More flexible sealing with the flow-wrapping machine from Schubert
The sealing technologies in the Flowpacker
Contact