Sealing systems for all flowpack films
Future-proof thanks to flowpack sealing
Manufacturers who pack their products into flowpacks are facing a trend towards more sustainable packaging materials, as is the entire packaging industry. Even if impermeability and other barrier functions of flowpack films cannot be easily achieved with every material, new variants such as mono films or paper-based films are already being used in addition to the classic composite films for heat-sealing and cold-sealing. Due to their material composition, however, the new films usually require extremely gentle sealing. Those who want to ideally position themselves for the future with sustainable packaging materials need appropriate sealing systems for their flowpacks. Optimum flexibility is offered by flow-wrapping machines which are able to seal the proven composite films as well as the latest, more sensitive flowpack films and to switch quickly between the two sealing systems.
This flexibility is already integrated into the Flowpacker, Schubert’s flow-wrapping machine, thanks to its variable sealing system. The technology combines the ultrasonic method for longitudinal sealing with cross-sealing, whose sealing time can be adjusted exactly to a constant value thanks to the flying cross-sealing unit. The advantage is that both longitudinal sealing processes are very gentle, and are not only suitable for heat-sensitive products but also for sustainable flowpack films. This is because with ultrasonic technology, the film is only heated where it is necessary for sealing. Sealing with ceramic heating elements is similarly gentle, because they enable a precise and controlled supply of heat, both in terms of temperature and duration. With cross-sealing, the constant sealing times ensure a consistently high sealing quality, regardless of production fluctuations. The unique sealing system is suitable for all types of heat-sealing films. Manufacturers benefit in several ways: greater freedom in the choice of their flowpack films, higher quality in the finished packaging and enhanced future prospects on the market.
New Box Motion cross-sealing technology allows even high-barrier films to be sealed with the highest quality.
Advantages of the flowpack sealing systems
Flexible packaging materials and high-quality sealing
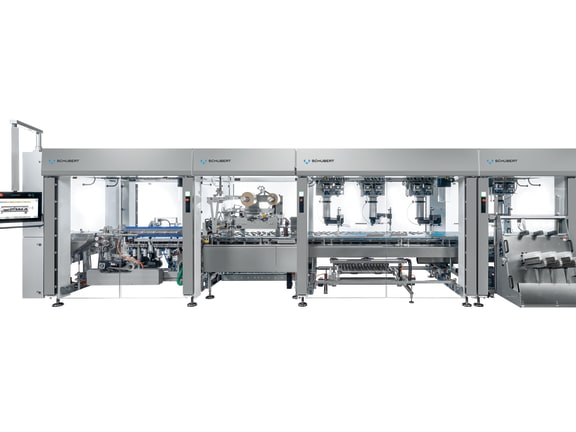
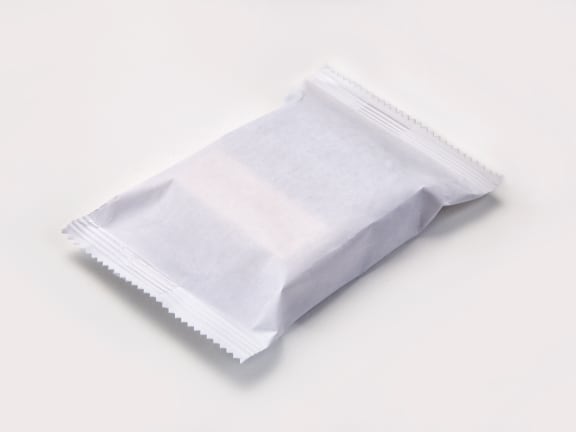
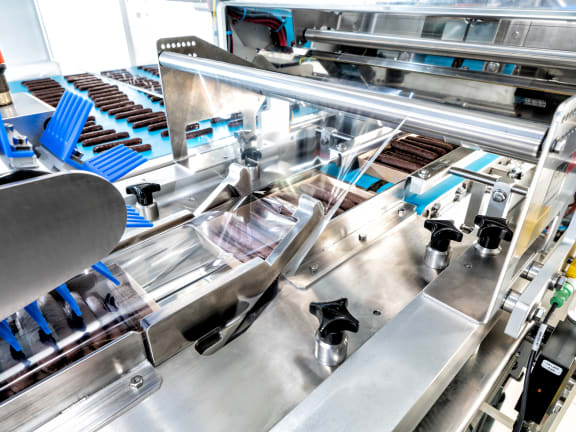
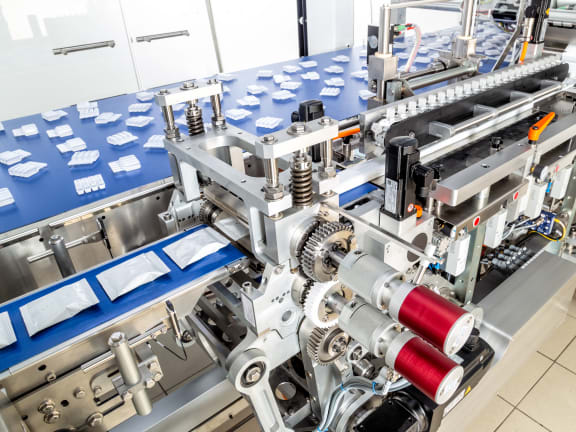
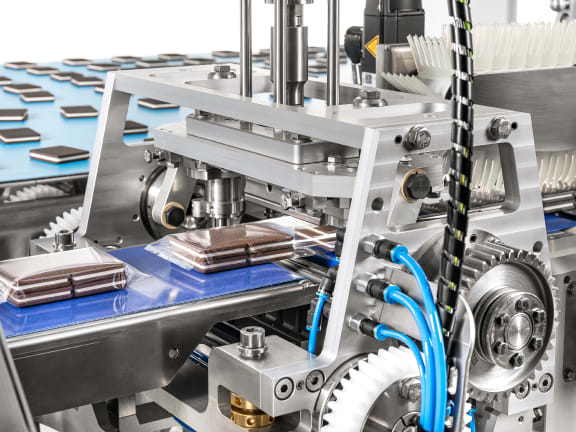
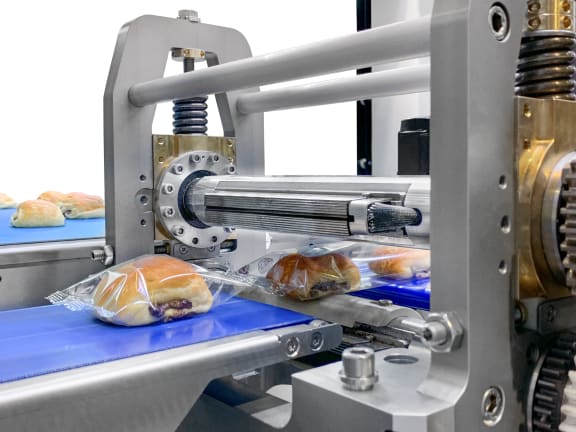
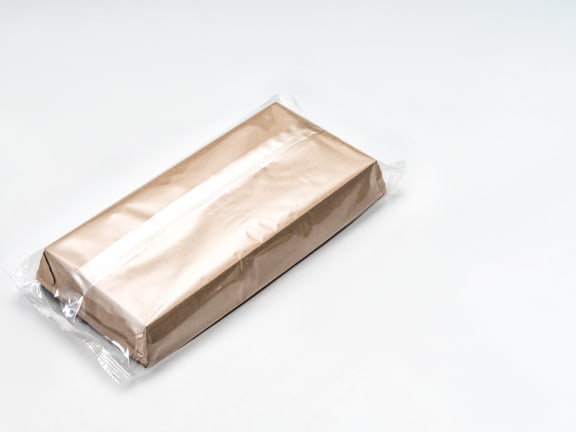
Flowpack sealing systems with Flowpackers from Schubert
Contact
Would you like further information?
Ask our team of experts!
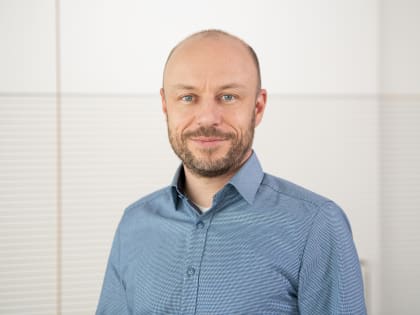
Stefan Horvath
Telefon: +49 7951 400-661