Modular packaging machines with built-in flexibility
How flexible robotic packaging machinery really is cannot always be seen at first glance. But at the very latest, at the second. For instance when the fast-moving packaging market demands new formats or new, more sustainable packaging materials. With a packaging machine from Schubert, manufacturers can rest easy. Thanks to the modular construction principle and the state-of-the-art robots developed in-house, flexibility is built into the TLM lines right from the start. This is what makes modular packaging machines from Schubert so efficient, sustainable and cost-effective in the long term.
As a leading manufacturer of modular packaging machines, Schubert pays the utmost attention to optimised seamless process chains and packaging technology that is one hundred per cent tailored to the specific needs of the sector. Behind this are the decades of research to optimise our packaging machinery as well as the ingenuity of an innovative industry driver in developing elegant and successful packaging solutions. That is why packaging machines from Schubert not only ensure extremely high availability, but are so flexible that they can even process conventional and new packaging materials on the same line.
Sub-machines
TLM sub-machines are constructed from the system components. The term “sub-machine” is a new one in engineering. It refers to self-contained, fully functional machines that incorporate one function of a complex packaging machine.
When TLM sub-machines are lined up and connected electrically, pneumatically and mechanically, they come together to make the TLM packaging system. The smallest TLM packaging machine might consist of a single sub-machine. On average, however, TLM machines are made up of 5.5 sub-machines. Large packaging systems bring this up to 11 to 15 sub-machines, and the largest system built to date is made up of 26 sub-machines.
Technology system components
Behind the packaging machines are the system components: highly flexible components such as robots for special tasks, the Vision System, our Transmodul transport robot, the Flowmodul flow-wrapping machine and the VMS packaging machine control system, which Schubert is continuously developing further.
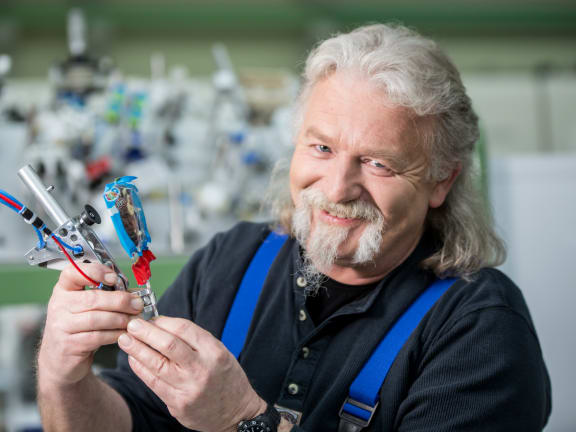
Functions
Our solutions make it possible to erect, fill, close, label, palletise, thermoform, flow-wrapping, box pack, wrap and perform many other special functions.
Contact
We can also package your product!
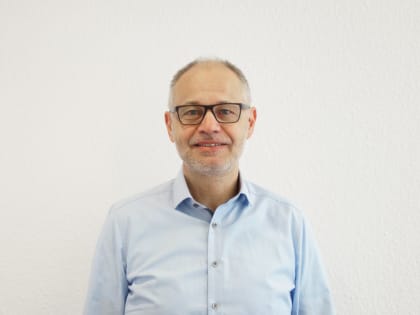
Describe your requirements to us in a no-obligation conversation. Simply make an appointment for a consultation now!
Efficient Packaging machines
With our Schubert lightline machine series, you can master standardised packaging tasks with great efficiency and high quality – at attractive purchase costs.
The series consists of packaging machines with preconfigured machine modules. This enables quick planning and assembly processes. A key benefit is that the packaging machines from the Schubert lightline product family are ready for use within a very short time. All machines are delivered in the high Schubert quality you expect: proven functional principles and the intelligent machine control system ensure reliable operation with high system availability over the entire lifecycle of the machine.