Manufacturers who want to survive in a fast-moving industry have to continuously adapt to the packaging requirements of the retail trade and therefore as a rule have to constantly invest in new packaging solutions. This is especially true for the FMCG sector. With this level of required flexibility, it is not easy to remain cost-effective in the long term. With the Flowpacker, Schubert delivers a unique answer to the major market challenges: The Flowpacker propels manufacturers into a new dimension of flexibility and offers them strong competitive advantages. The Flowpacker is a packaging machine which can adapt to all current and future trends over many years, making it a secure investment.
This is made possible by the unique machine concept: The Flowpacker from Schubert fully integrates the packaging process into a slim TLM line and combines it with upstream pick & place robots instead of long infeed belts. This combination of packaging functions and the integrated solution saves up to 70 per cent space in production. The system is many times more efficient than conventional flow-wrapping machines, since the entire packaging process runs without interfaces. So once again, Schubert’s tried & tested modular technology offers decisive advantages for the Flowpacker: Maximum flexibility, top quality and maximum efficiency.
Flexibility when packing into flowpacks – easier than ever before
A flow-wrapping machine with high flexibility enables manufacturers to respond quickly to new market requirements. And not only to clearly recognisable trends such as new materials and a wide range of formats, but also to future developments that are not yet foreseeable today. The greater the choice of products, materials, packaging formats and sealing technologies, the greater the probability of being ideally prepared to take on new tasks. Switching quickly between the most diverse formats is easier than ever with the Flowpacker.
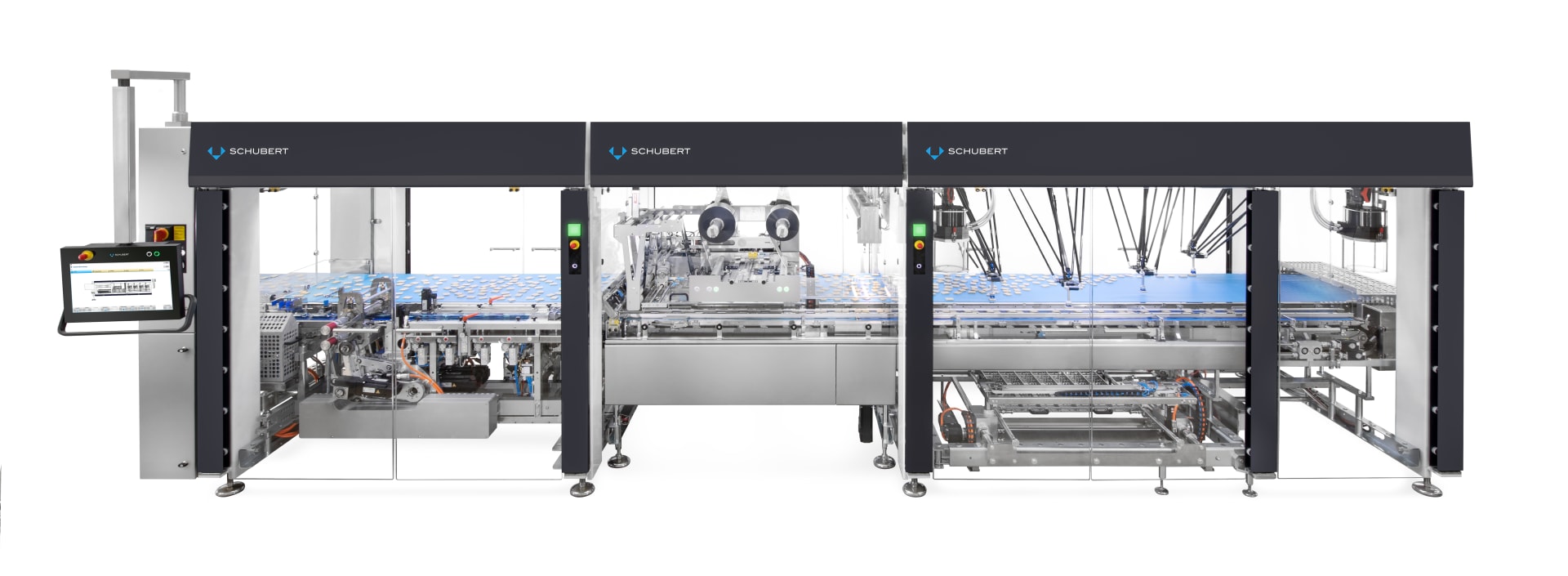
The Flowpacker is many times more efficient than conventional flow-wrapping machines, as the entire packaging process runs without interfaces.
Highly flexible format changes with the Flowpacker
Composite films, recyclable mono films and paper-based films can be processed on the same line.
- The pick & place robots can pick up every conceivable product from the food, confectionery, pharmaceutical and cosmetics industries.
- Naked products or products placed in trays can be packed into flowpacks. As an alternative, U-boards or flat boards made of cardboard can be used. Virtually all product configurations are possible.
- Thanks to individually developed high-quality forming shoulders, the Flowpacker processes all packaging materials: composite films as well as recyclable mono films or paper-based films.
- Schubert enables both cold-sealing and its unique heat-sealing technology on the same line. An optional ultrasonic sealing unit is also available for the longitudinal seam
- All format changes for carriers, robot tools, forming shoulders, film rolls or sealing technologies can be carried out quickly, partially automated and with a few simple steps.
- The flow-wrapping machine’s output is scalable by different speeds, individually switchable pick & place robots, and easy extension with sub-machines.
High product quality – consistently achieved in the packaging machine
Quality is inextricably linked with Schubert, also with the Flowpacker. Even the Flowpacker’s machine concept stands for outstanding product quality. This is because packaging with pick & place robots is much gentler on sensitive products than conventional feeding of the goods over long belts. Integrated quality control guarantees that only perfect products are packed into the flowpacks. Due to the unique sealing technology, each individual flowpack is sealed optimally. At the end of the flow-wrapping machine, a high-quality product leaves the line in a perfect package.
Achieve the highest product quality with the Flowpacker
- Pick & place robots eliminate the need for long, product-damaging transport routes via infeed belts.
- Thanks to individual tools, the pick & place robots handle each product extremely gently. For unusual product shapes, Schubert offers precisely fitting 3D format parts.
- Schubert’s image recognition system ensures that only flawless products are allowed to be packaged in order to meet the manufacturer’s quality features in every package.
- The high-quality sealing technology provides optimally sealed flowpacks for cold-sealing and heat-sealing.
- The flying cross-sealing unit enables precisely selectable, constant sealing times to be achieved for a perfect sealing seam.
Efficiency in the packaging process – maximised by the machine concept
The more efficient it is, the more cost-effective it is: The Flowpacker fulfils this equation in many respects. The integrated Flowpacker is unbeatably compact and makes all format changes much easier thanks to its interface-free concept. Because the safer and faster a format change can be carried out, the sooner the packaging process starts again in high quality after the change. This is why robot tools, sealing technology or packaging material can be exchanged with just a few simple steps and partially automated. This has been Schubert’s philosophy for decades – and it is reflected in the Flowpacker. Comprehensive OEE evaluation via the Schubert GRIPS.world platform also ensures optimum machine efficiency over the long term.
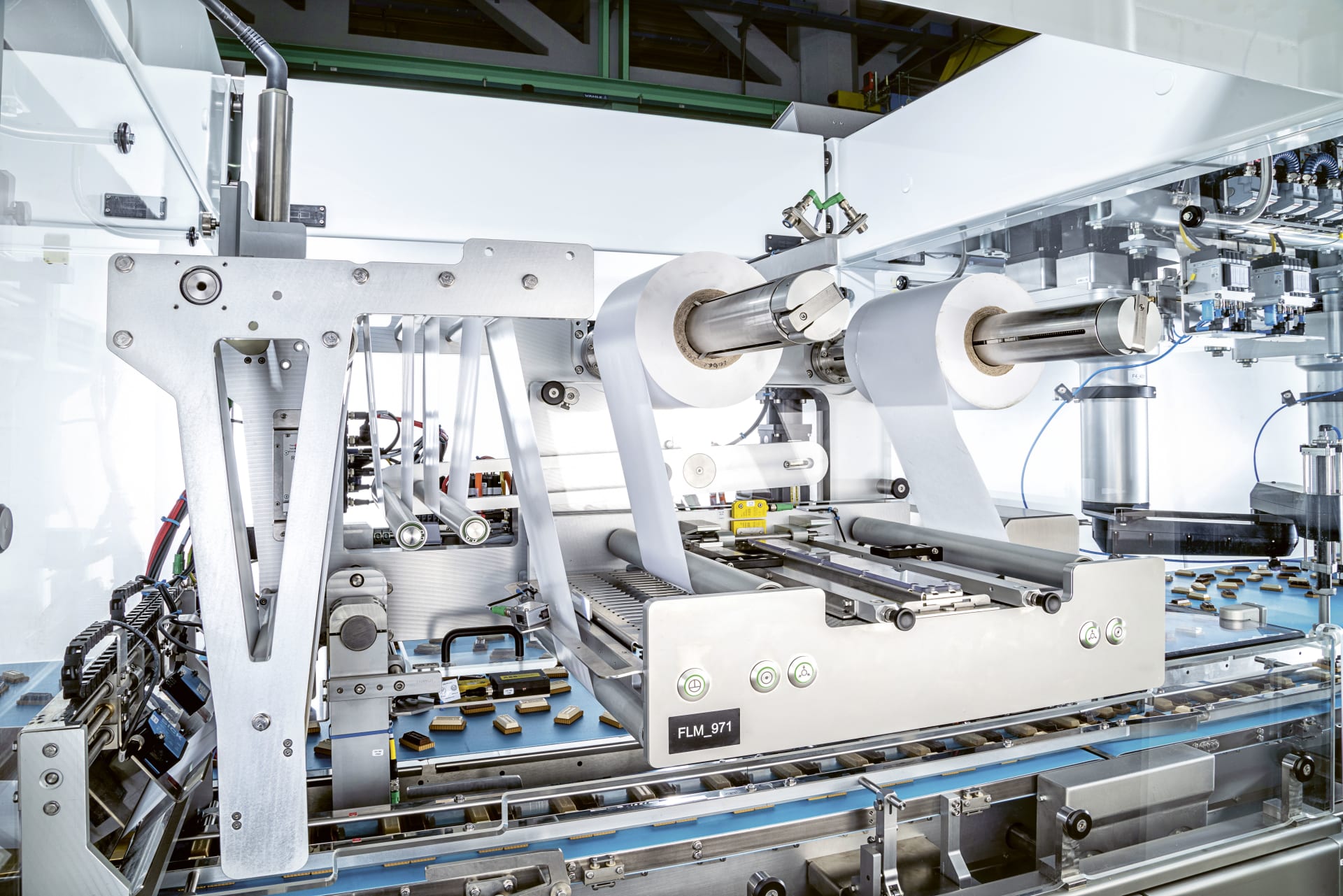
Automated and safe format changes such as the automatic ‘chain flight’ changeover or the automatic change of the film reel ensure fast start-up times without losses.
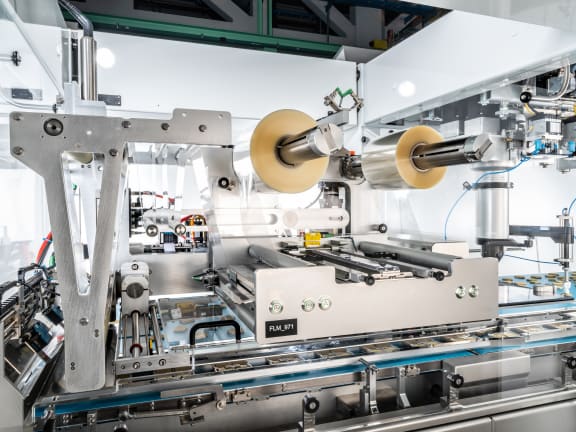
Automated and safe format changes such as the automatic ‘chain flight’ changeover or the automatic change of the film reel ensure fast start-up times without losses.