Packaging robots: automation for the packaging industry
Bottlenecks in modern robotic packaging machines are definitely a thing of the past. With packaging robots, even complex tasks such as pick & place, changing product assortments and several process steps in a single line are easily mastered. Cobots, for example collaborating robots outside the lines, are also conquering the packaging industry. Schubert is your ideal partner for advanced robot technology: We have been spearheading the industry for decades with our packaging robots developed in-house – with customised tools, of course. Optimised to meet the very specific requirements in the packaging industry and ready for any application, Schubert robots bring more flexibility and reliability to your automated packaging – so that you can always rely on your packaging processes.
Robot technology for every application
Our packaging robots are exceptionally versatile co-workers that ensure controlled processes at a consistently high level inside, and with the tog.519 cobot also outside, the packaging machines. The automation solutions range from erecting, filling and closing or sealing a wide variety of packages, to pick & place applications and sealing flowpacks, to line integration of several packaging steps with Schubert’s Transmodul transport robot.
Expertise
Schubert – the trailblazer in packaging robots
With Schubert, you’re working with the best possible partner. We were the first company in the world to develop and produce packaging robots for the packaging industry ourselves. Our credo is “From professionals for professionals”. Packaging robots from Schubert are designed to address the most pressing challenges faced by all FMCG companies that package food, cosmetics or even technical products: high cost pressures, shortages of skilled workers and the efficient use of raw materials through seamless quality control and minimisation of rejects. You’ll greatly benefit from smooth processes with a high degree of flexibility, even in terms of packaging types.
Thanks to in-house development, we ensure that all requirements can be met. Consistent digitalisation and customised adaptations of tools further boost our customers’ competitive advantage. Every day, an average of four new Schubert packaging robots are put into operation somewhere on the planet. That’s over 1,500 units per year.
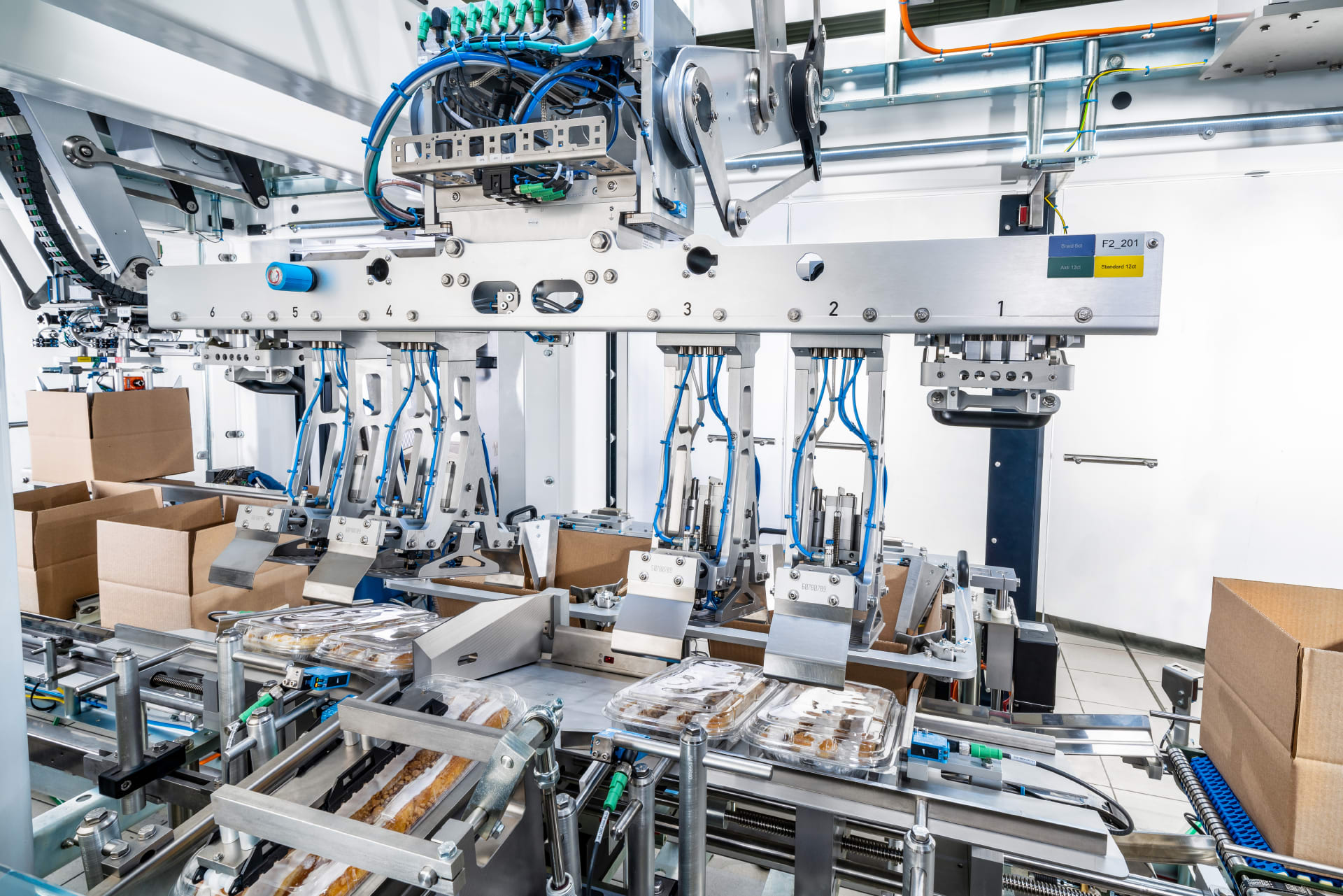
Schubert Motion: Cutting-edge motion development
We are absolutely certain that the future lies in achieving the ideal combination of people, sensor technology, AI and robotics. And this is exactly what our Schubert Motion department in Dresden focuses on. At the dedicated location, our team specialising in robotics and AI uses state-of-the-art technologies to develop software for optimising our robot movements. Digital mapping of entire packaging processes, the networking of more and more machines and the evaluation of results by AI open up entirely new horizons when it comes to increasing efficiency. This applies to improving performance as well as energy consumption, where savings of up to 20 per cent can be achieved. That’s why we are constantly developing not only our robots, but also our in-house cloud and IoT solutions.
A comprehensive system solution
Packaging is teamwork
Our packaging robots can do a lot, and there are so many of them available to you. But what really makes them unique is that they form a perfectly coordinated system thanks to the control and image processing software we also developed in-house. One that not only boosts the quality of the packaging process to a new level, but also its flexibility. Quite simply because Schubert robots work exclusively with our customised tools.
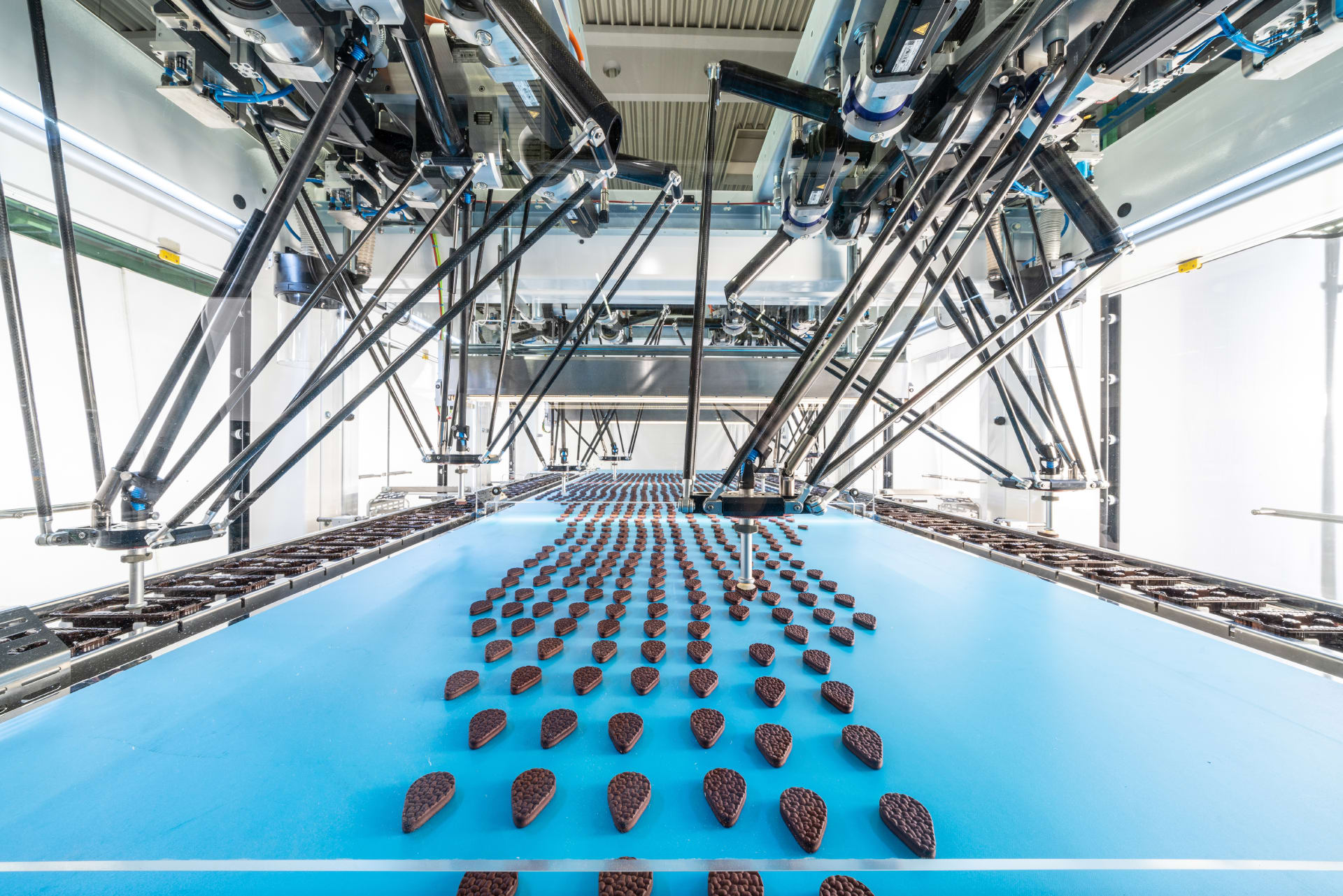
Brains made of silicon: the control technology
To ensure that our packaging robots do exactly what they are supposed to, a lot of different information needs to be processed in the shortest possible time. Our vision system ensures the right image processing and our control system ensures the right implementation. And we use AI to make programming even easier in the future. Neural networks are already helping optimise robot paths with Schubert Motion and program the cobot. This creates solutions that greatly increase your competitiveness.
The watchful eye for quality: our vision system
The pick & place vision system recognises not only the quality, but also the position of products faster than a human being ever could. Even 5,000 products per minute are never a problem for our scanners with a working width ranging from 200 to 1,800 mm. And whether via incident light or 3D scanner, only flawless products are reported to the packaging robots and picked up by them. By detecting rejects in good time, you save time and money. Our systems are also skilled in the fine art of image processing – reaching into the disorder. We use this with the cobot, for example.
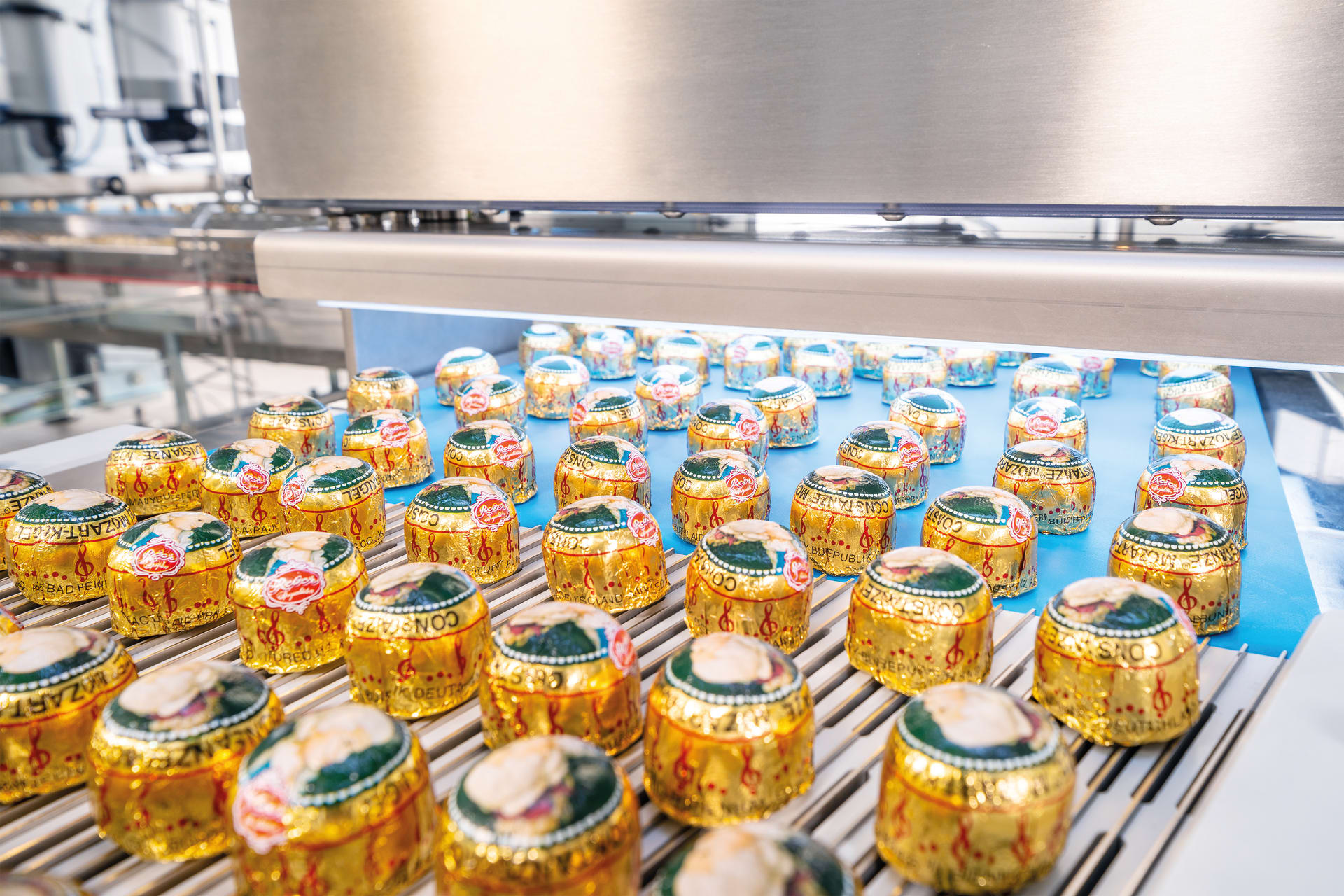
Customised is always better: our robotic tools
Automation with robots makes a decisive contribution to your competitiveness. A smooth process flow, however, also calls for quick tool adjustments when changing formats and, above all, the right tools to ensure gentle handling. This is never a problem with Schubert packaging robots: Changing formats couldn’t be easier with our tools – and the packaging machine can then restart immediately with the highest level of precision. Thanks to individually adapted format parts, and of course even for delicate and fragile goods, with a minimum of waste. And you can now conveniently print new format sets or replacement tool parts in the highest quality on your premises.
Print 3D format parts yourself with the PARTBOX
Schubert also offers the real deal when it comes to tools: Whether greasy, crumbly, sticky or fragile products – we will design the perfect robot tool for your product and your application. Benefit from our experts’ many years of expertise, increase the efficiency of your operations and eliminate sources of error right from the start. With PARTBOX, you also gain access to your 3D format parts for self-printing – directly from our streaming platform to the PARTBOX printer on your premises. Of course, we will also supply you with the suitable raw material for additive manufacturing. No waiting times, no delivery bottlenecks – simply quick format changes with your perfectly customised tool.
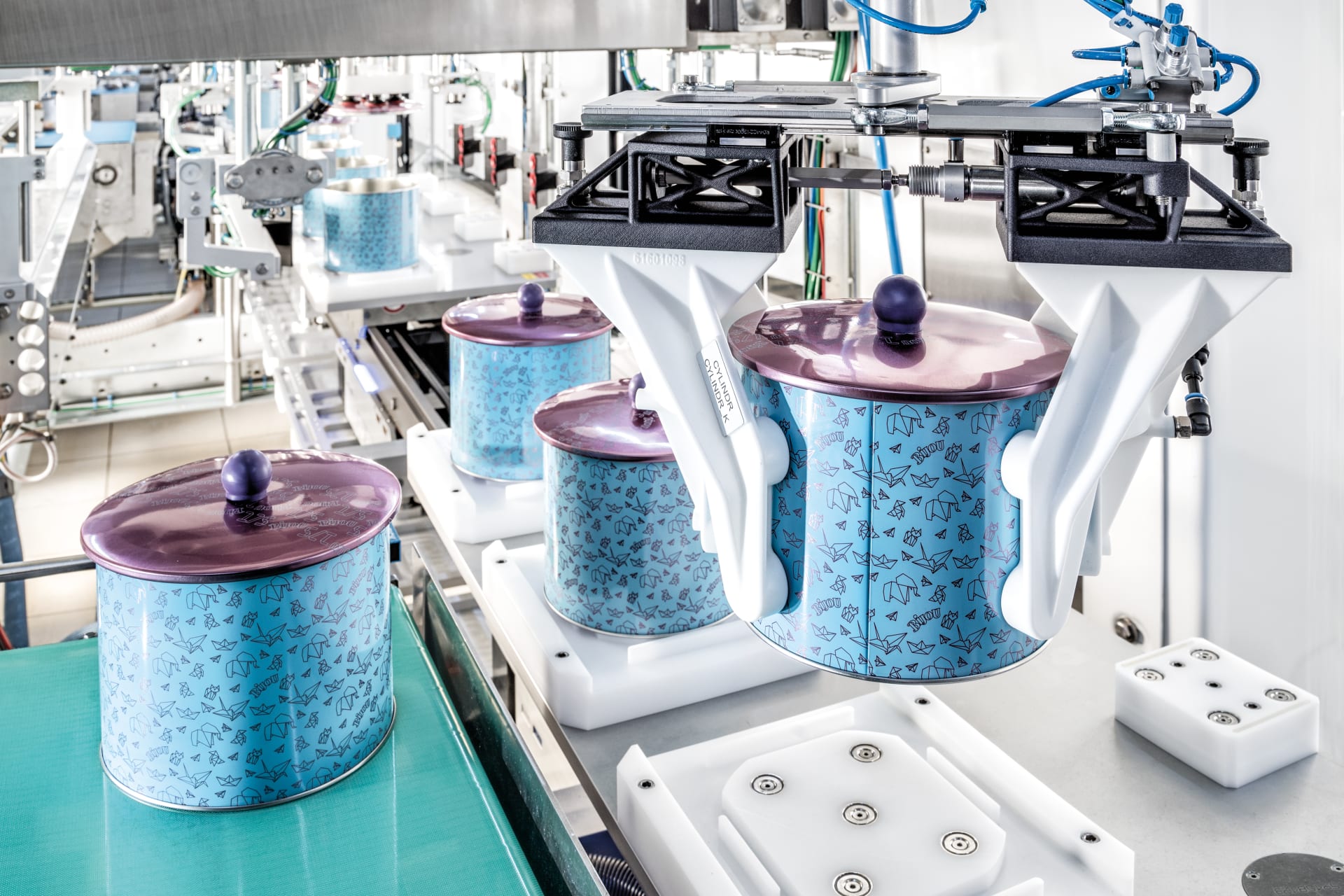
More sustainability thanks to automation
At Schubert, we are well aware of our responsibility towards nature, the environment and, of humankind. This is why sustainability not only plays an important role for us, but it has also become the cornerstone of everything we do. Thanks to our automation solutions with state-of-the-art robot technology, we can also support you on your way to a sustainable future. Whether to prevent rejects, save energy or make better use of resources, whether to use sustainable packaging materials or to ensure recyclability – you've come to the right place if you’re looking for greater sustainability in your packaging processes!
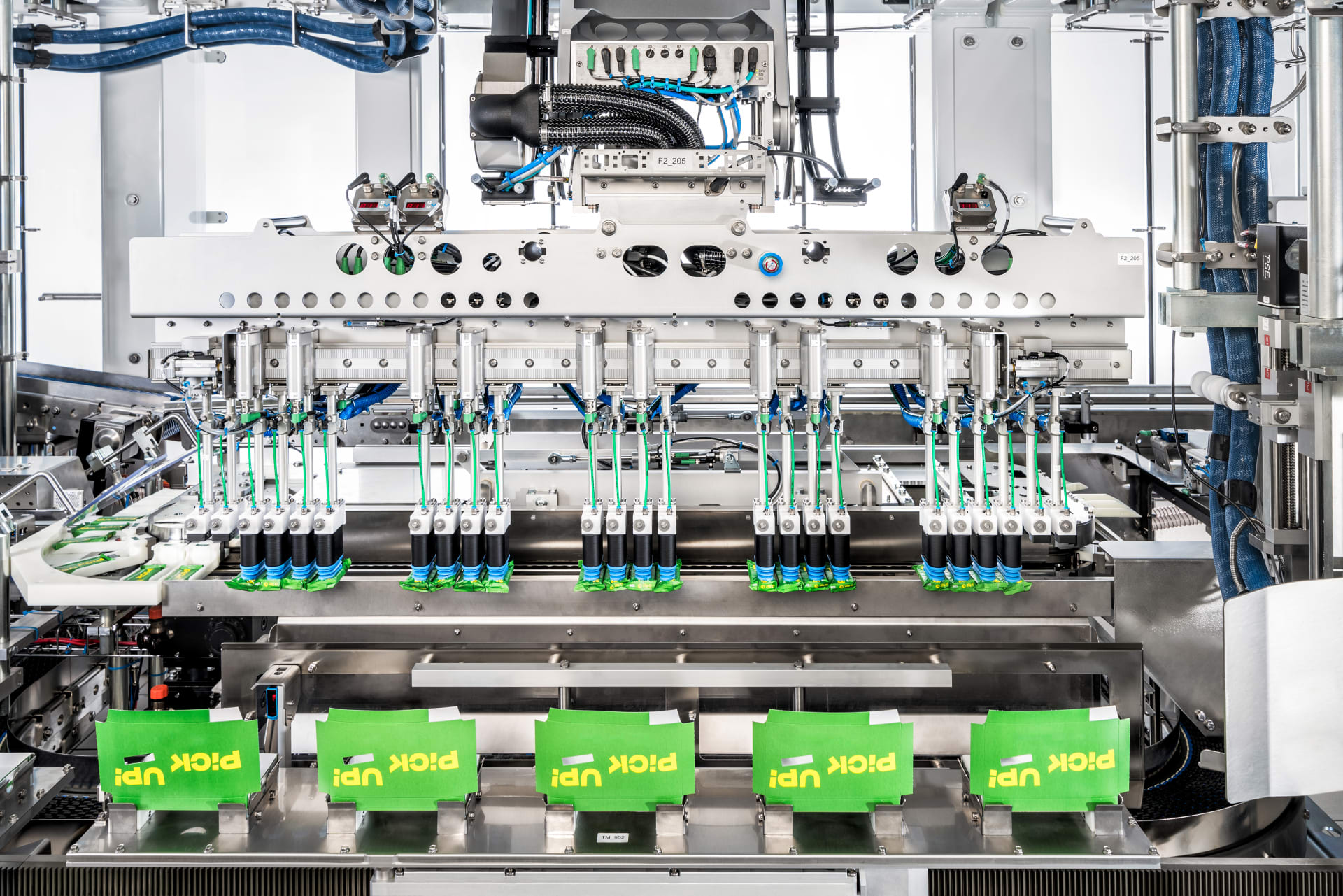