The flow-wrapping machine from Schubert – developed for the future
End-customers and retailers are calling for ever greater packaging variety. At the same time, packaging and materials need to become significantly more sustainable for the future. These trends demand the shortest possible response times from manufacturers and very rapid adjustments to the market. This can only be achieved with highly flexible packaging machines. With the Flowpacker flow-wrapping machine, Schubert is offering an integrated machine solution that opens up a new era of flexibility and future-proofing.
Compared with conventional machine solutions, the Flowpacker saves up to 70 per cent space in production. At the same time, customers benefit from extraordinary flexibility: Virtually any type of and rapid changeover between sealing technologies, product formats, or proven and new packaging materials is possible. This all contributes to making the packaging machine much more cost-effective in the future. With the Schubert Flowpacker, manufacturers can now adapt much more flexibly and sustainably to the needs of consumers and the trade, thereby creating new market opportunities and competitive advantages.
Learn more about our the lightline flowpacker advantages in our new web-seminar series Schubert4You
Kontakt
Do you find our integrated solution exciting? Talk to our flow-wrapping machine expert.
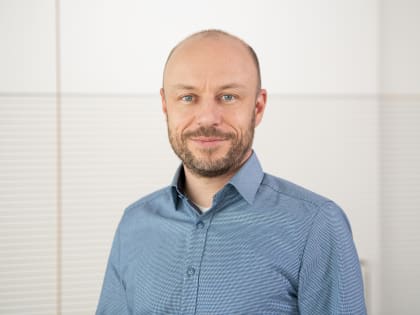
Stefan Horvath
Telefon: +49 7951 400-661Were you not able to reach us? We will gladly call you back at the time you request!
Flow-wrapping machines with robots – a quantum leap in packaging technology
Improving packaging processes in the interest of the customer – has always been the mission and goal of Schubert and is today pursued by the third generation of the family-owned packaging machine manufacturer. With each of its innovations, Schubert not only wants to pick up on market trends, but also to optimally meet its customers’ needs for efficient, compact and interface-free solutions. Part of this success is an approach that the founder, Gerhard Schubert, pursued back in the 1980s: packaging with the aid of robots. Schubert’s developers and machine builders are always picking up on impulses from the field of robot technology. And all these strengths come to fruition with the Flowpacker flow-wrapping machine.
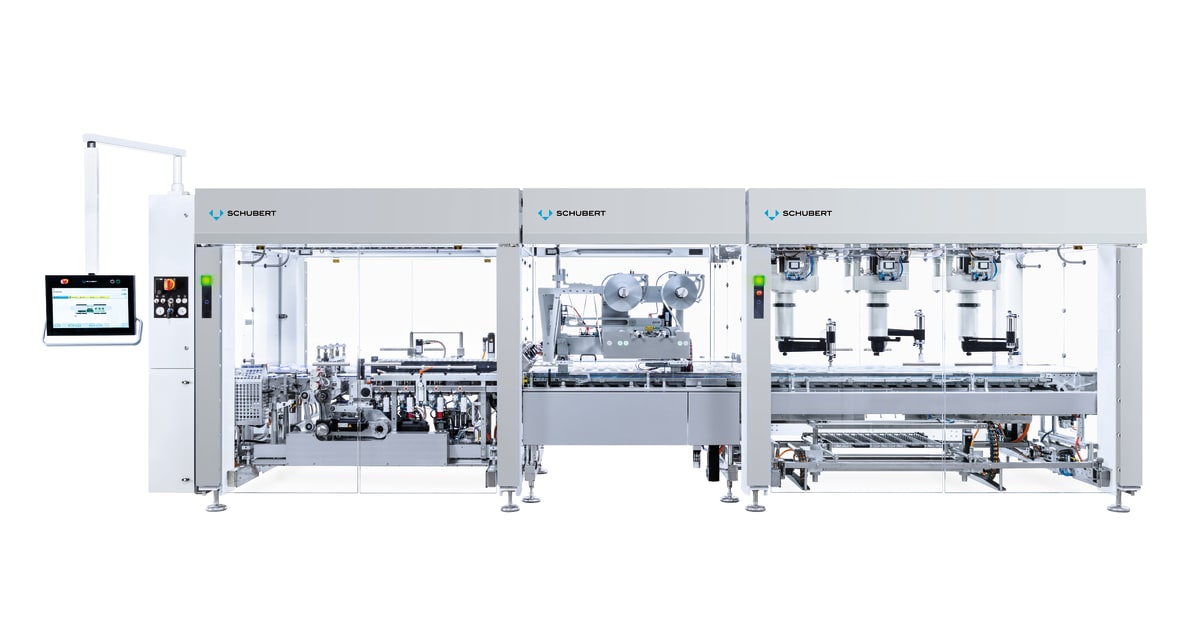
Safeguarding the future through high flexibility
Product, packaging material and sealing technology are all up to you - you decide
The flow-wrapping machine’s integrated concept offers customers outstanding flexibility on several levels. The use of pick & place robots for feeding ensures that a wide variety of products can be packed. This includes especially sensitive goods that crumble quickly, are fragile or sensitive to heat. Additionally, the variable robots allow a wide range of packaging formats with and without trays to be used. The number of active pick & place robots in a line can also be varied depending on output requirements.
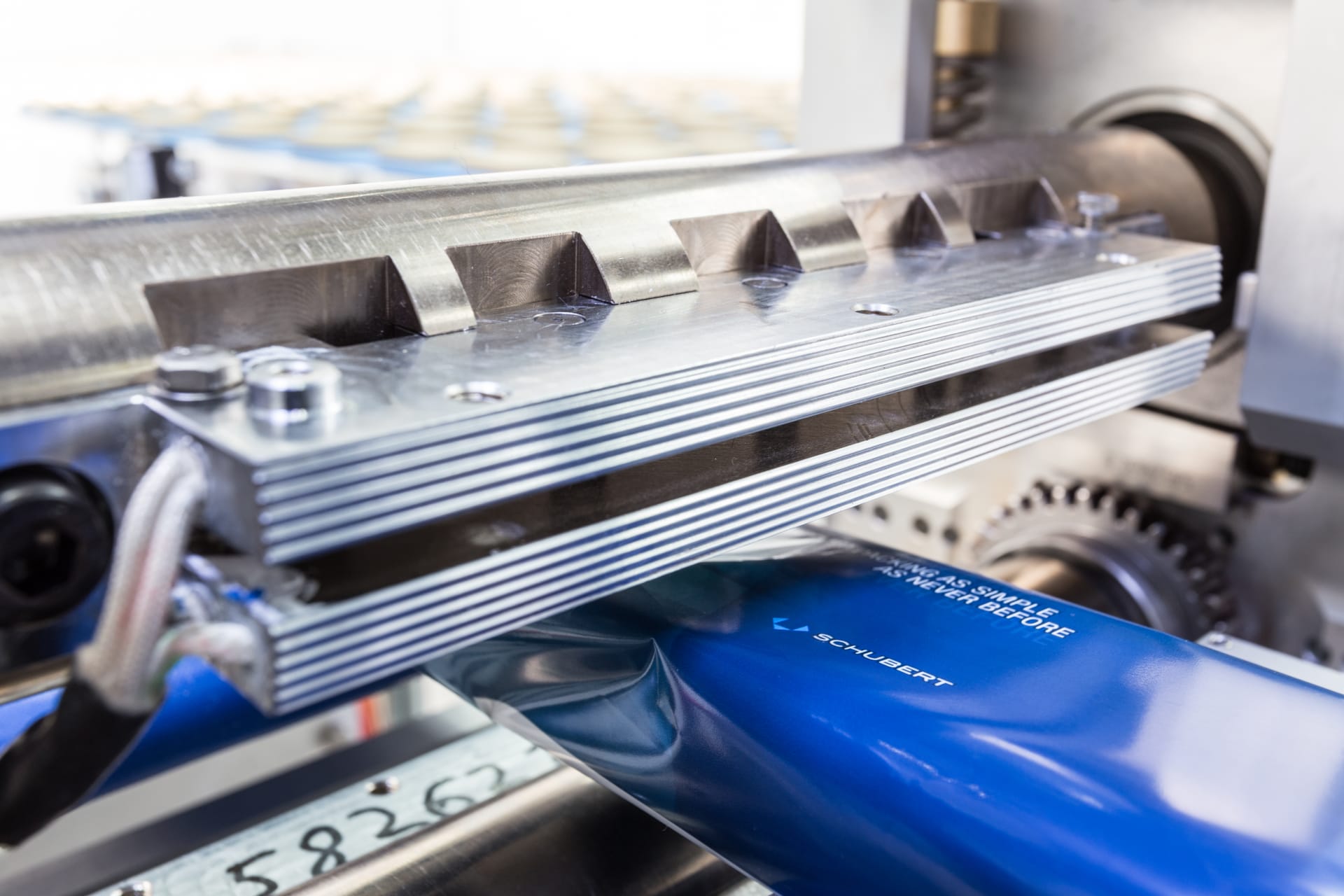
More flexibility, more quality, more efficiency
Ten key advantages of the Flowpacker
More flexibility through
- proven and new packaging materials, including sustainable films
- a wide variety of product formats, including highly sensitive products
- diverse packaging formats, with and without a tray
- changing between cold- and heat-sealing on one machine
More quality through
- high sealing quality due to unique sealing systems,
- product-friendly packaging thanks to feeding with pick & place robots
- quality control of all products via image recognition with the Pick and Place Vision System
More process efficiency through
- extremely fast format changeovers for product, packaging and sealing technology
- compact machine layout with significant space savings
- high machine efficiency thanks to OEE evaluation
Complete solution from Schubert for packing frozen pancakes into flowpacks.
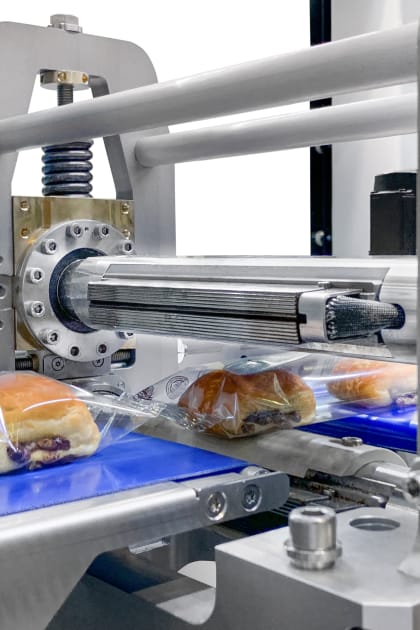
“It’s fascinating that we can now package numerous products and formats on a single line. This is very reassuring for me as Managing Director. I am convinced that with Schubert we have the right partner on our side. Thank you, Schubert!”
Serge Bohec
Managing Director of La Petite Bretonne
Product configurations with the Flowpacker
With the integrated solution from Schubert, virtually all product configurations in flowpacks are possible. The pick & place robots process naked products or products already packaged in primary packaging, and pre-group them in numerous variants for the flow-wrapping machine. Single, stacked, side by side or on top of each other, with or without trays – the possibilities are close to endless.
Case Studies
Which application(s) is(are) interesting for you??
Ask us specific questions about your project, we will be happy to advise you! Please send us an explanatory sketch or a photograph with your inquiry. Our experts look forward to supporting you in the context of a personal meeting.
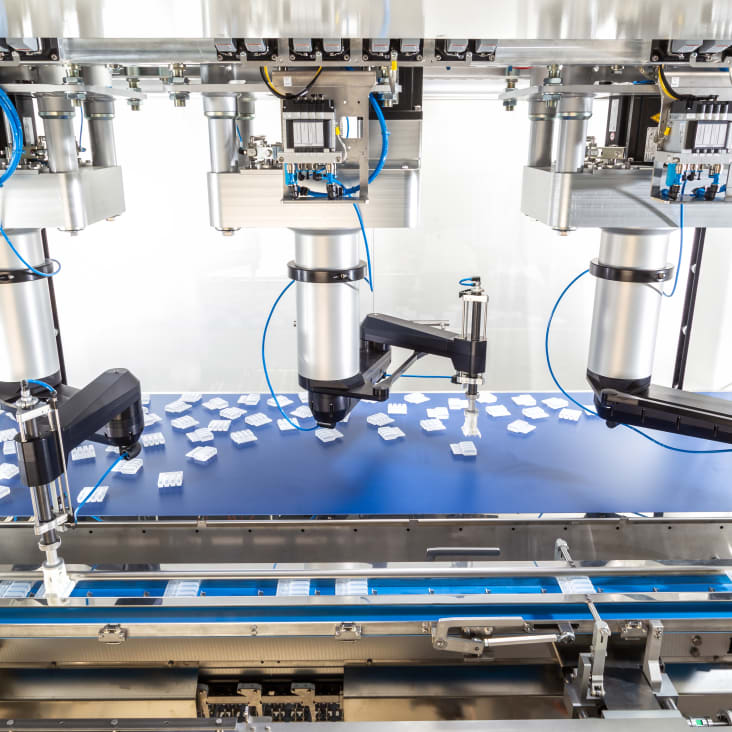
Technical Details
A modular flow-wrapping machine of your choice
The Flowpacker flow-wrapping machine consists of at least three and up to any number of TLM modules. The horizontally positioned flow-wrapping unit is fully integrated into the TLM modules. A freely selectable number of pick & place robots is located upstream. Depending on performance and space requirements, either the proven F4 robots or the T4 and T5 robots from Schubert based on the delta design can be used. The flow-wrapping process is fully integrated into the line, making the machine layout extremely compact.
Feeding with pick & place
For the packaging process, the naked products or products already provided with primary packaging are fed to the system on a belt. An image recognition system with a 3D scanner checks position, orientation, shape, colour and volume. Only perfect products are then processed by the pick & place robots. With their individually designed tools, the robots pick up the products gently and, depending on the format, group or stack them in the chain or in prepared trays. Thanks to the exchangeable robot tools and carriers, product or packaging format changes can be implemented quickly and easily.
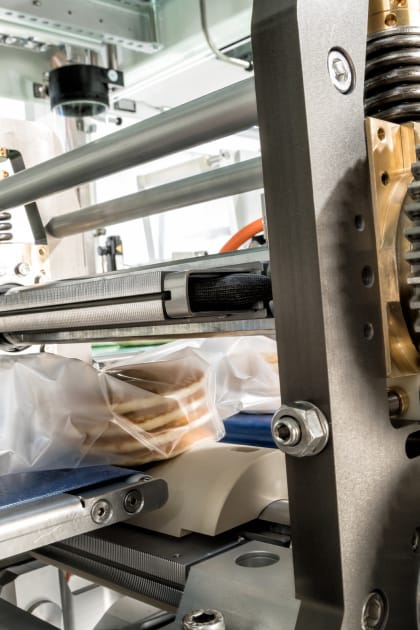
“The ability to package different products and formats with just one machine was a key reason for choosing the complete solution from Schubert.”
Dumas Garrett
President and CEO of De Wafelbakkers
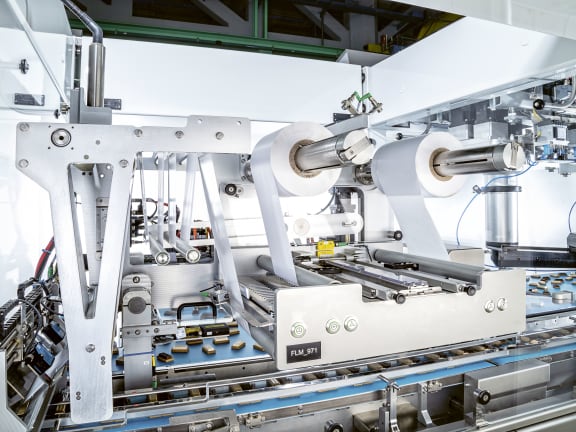
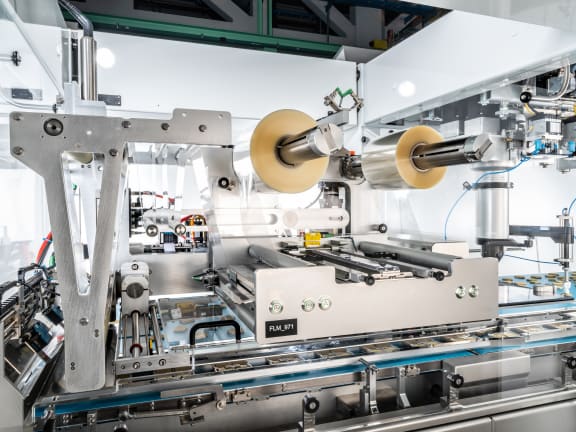
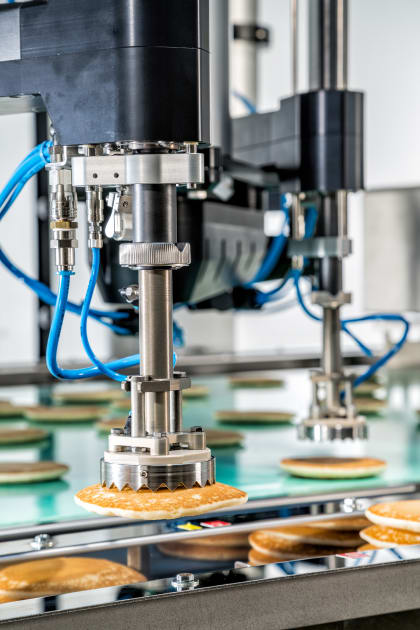
“Our customers associate our name with the highest product quality and product variety. The goods that we sell must therefore be flawless.”
Don Ephgrave
Senior Vice President Operations, De Wafelbakkers
Technical details
- Combination of flow-wrapping unit and pick & place robots
- Compact machine layout due to an integrated flow-wrapping process
- Very high format variety for products, packaging and films possible
- Cold- and heat-sealing technology in one system
- Unique flying cross-sealing unit
- Optionally, F4 or T4/T5 robot
- Individual robot tools with 3D format parts
- Image recognition with 3D scanner
- Integrated GS.Gate with GRIPS.world platform
- lightline variant with half the delivery time available